Automotive Manufacturing - Lean Deployment
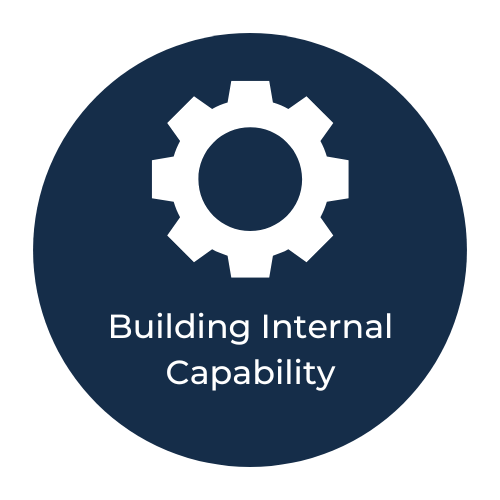
about this project
The client is a world leading manufacturer of automotive products with a client base including all major manufacturers in both the EU and USA automotive markets. The requirement for a Lean Implementation program was identified as being needed to completely review the end to end process set-up and effectiveness.
This Lean deployment project took place within a high-volume automotive manufacturing environment where production cells were operating at just 64% effectiveness. The client faced persistent quality issues, long set-up times and excessive batch sizes, all of which were impacting cost, throughput, and customer satisfaction.
Through a structured Lean deployment, supported by PBI’s Lean Practitioner and Business Transformation training courses, cross-functional teams were equipped with the tools and coaching to assess and redesign their production processes. Using techniques such as cellular manufacturing, SMED, and root cause analysis, the teams introduced more agile and efficient workflows.
The objective was to reduce waste, improve first-time quality, and create a sustainable culture of continuous improvement across operations. The result was a
major uplift in quality, faster changeovers, and multi-million pound savings delivered and sustained by internal capability.
Key Project Summary "At a glance"
Project Scope
- Process Improvement
- Product Cycle Time & Flow
- Product Quality
- Manual Handling
- Internal Transportation of materials
- Effective Team Working & Engagement
- Effective Leadership in changing environment
-
- Internal Capability Build
Improvement Strategy
- Sunrise Campaign Room meetings
- Visual Management
- Process Mapping
- Value Stream Mapping
- Kaizen Events
- Cellular Manufacturing Implementation
- Daily Huddles
- Capability Build Plan
Benefits Delivered
- Cellular Units delivered quality increase from 64% to 95%
- Print Set-Up reduced from 40 mins to 6 mins
- 60% Defects reduction during set-up
- 90% reduction in batch size
- Combined Quality improvement & Set-Up reduction. Cost saving pa: £2.72M
- Inspection defects reduced by 15%
- Internal Capability Build plan executed