Case Studies
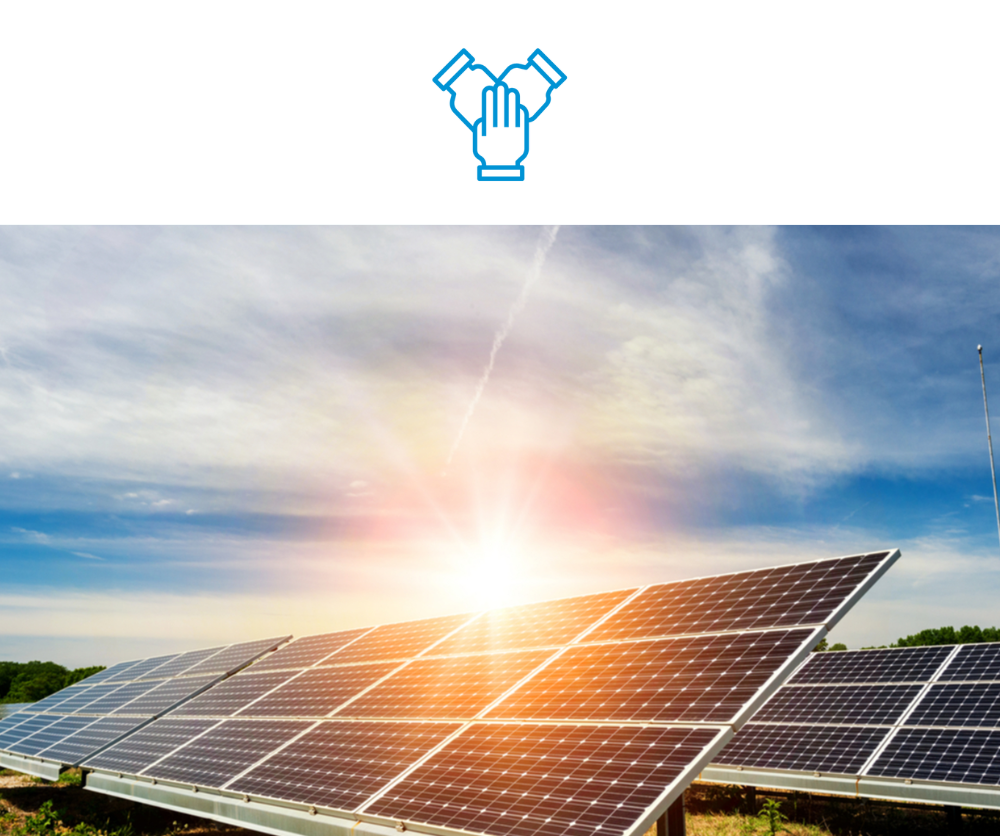
Engaged Culture (Renewables Industry sector)
Successfully implemented 70+ effective communication systems.
450+ people use effective collaboration tools daily
6.5k - 7.4k hours/pa saved ($462k) by reduced meetings.
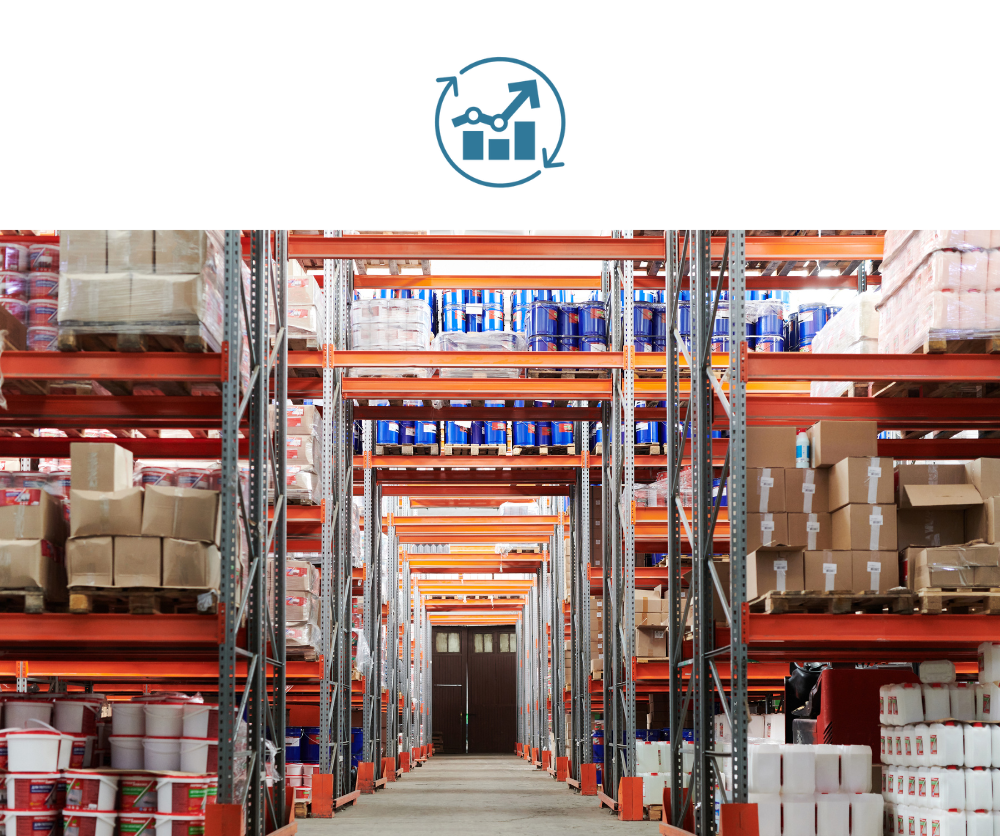
Purchase-to-Pay (P2P) (Energy Industry Sector)
5.4M cost OPEX reduction.
2000 hours removed from planning activities.
Reduction of £20M in materials stored.
Reduced warehouse storage by 40%.
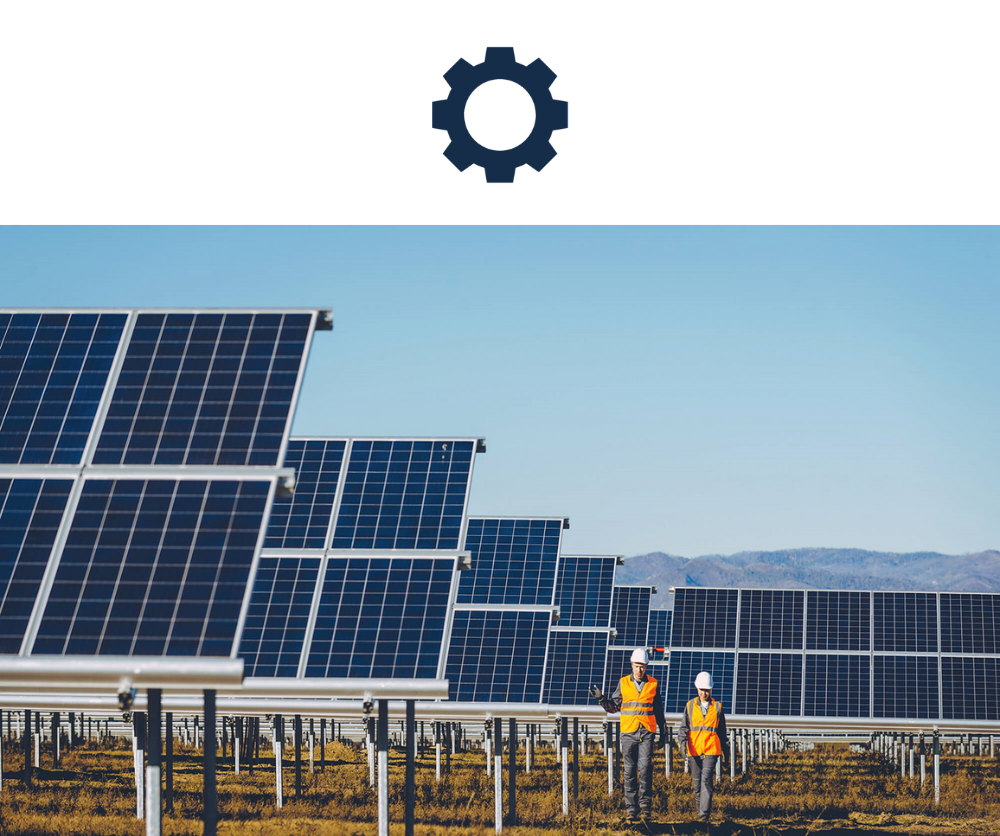
Internal Capability Build (Renewables Industry Sector)
6 Business Agility Knowledge full day courses conducted.
100+ trained staff now lead change efforts in their own areas.
14 countries supported.
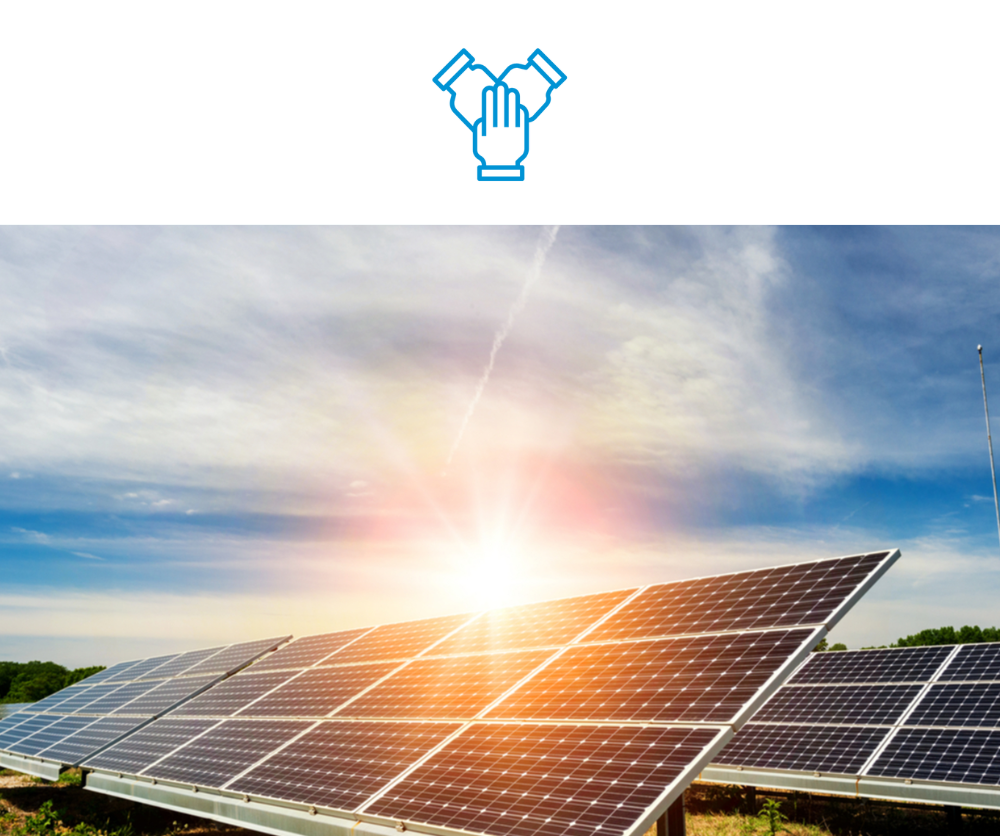
Engaged Culture (Renewables Industry sector)
Successfully implemented 70+ effective communication systems.
450+ people use effective collaboration tools daily
6.5k - 7.4k hours/pa saved ($462k) by reduced meetings.
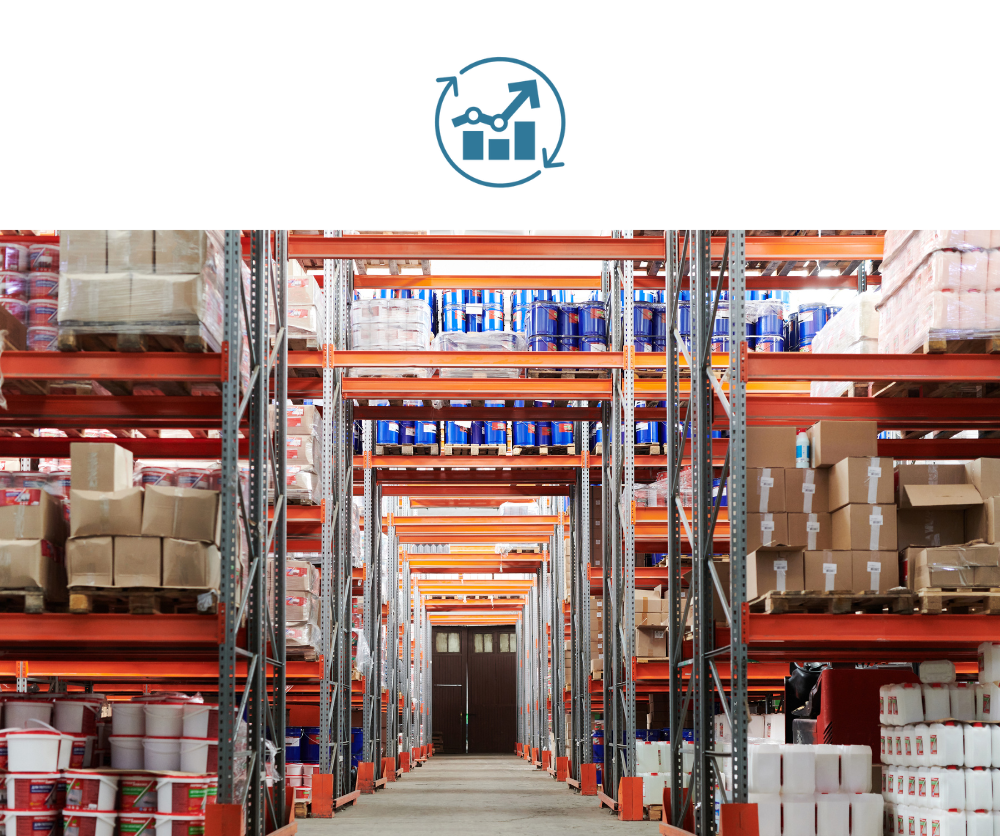
Purchase-to-Pay (P2P) (Energy Industry Sector)
5.4M cost OPEX reduction.
2000 hours removed from planning activities.
Reduction of £20M in materials stored.
Reduced warehouse storage by 40%.
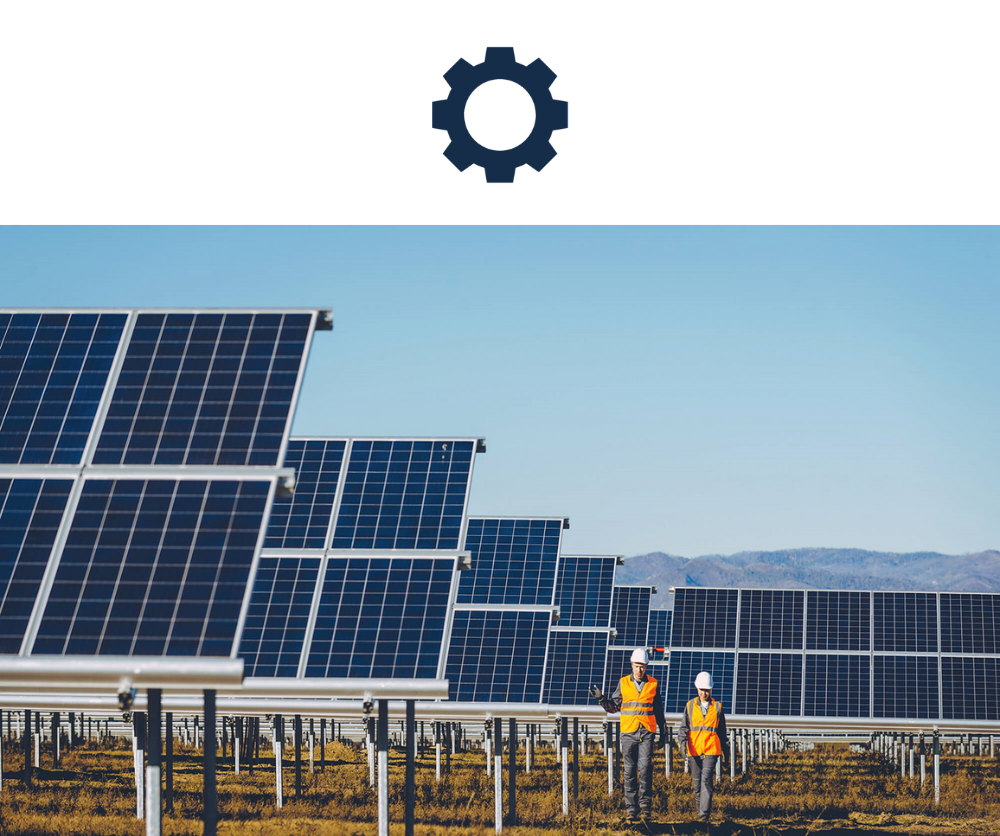
Internal Capability Build (Renewables Industry Sector)
6 Business Agility Knowledge full day courses conducted.
100+ trained staff now lead change efforts in their own areas.
14 countries supported.

Supply Chain Risk Management & Warehousing Consolidation (Energy Industry Sector)
$15.0M ($9.5M temp storage) made available on SAP to the business.
$1.4 M (Book value) Disposed.
Obsolete or Surplus Stock Removed.
$11.4M (GOI) Additional Inventory Disposed.
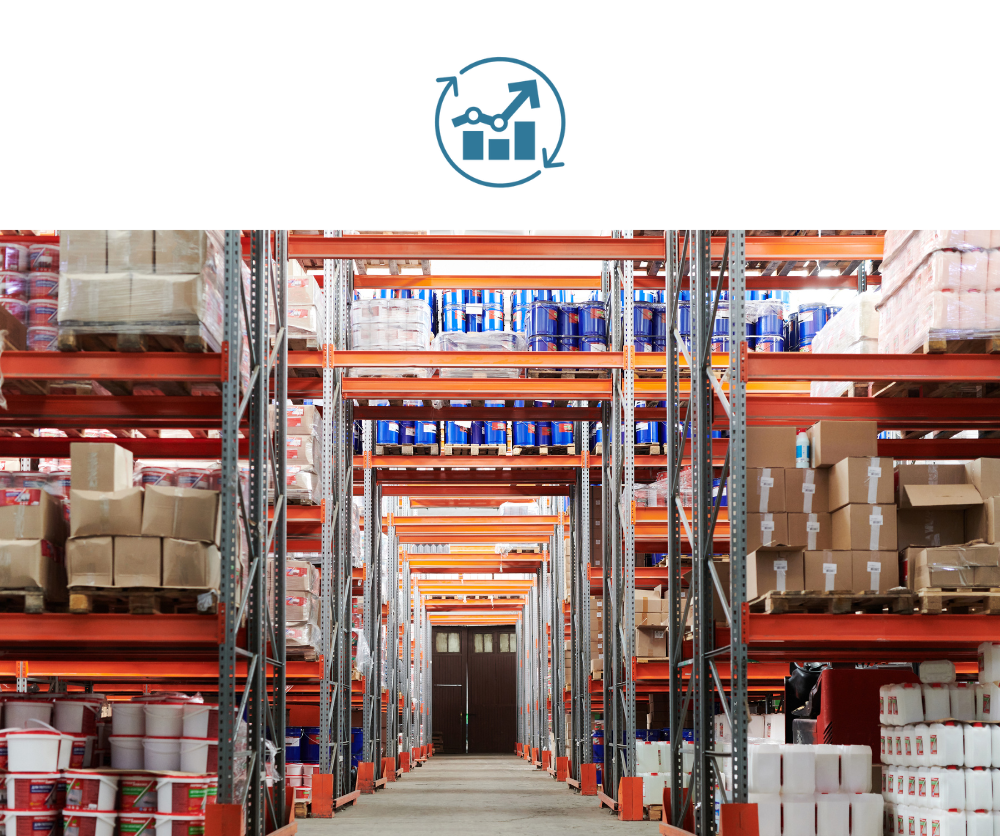
Manufacturing Programme of Improvements (Energy Industry Sector)
Production increase from 11.6M to 14.6M = 26% increase
People in this process reduced from 30 to 8 = 75% reduction
Working hours from 59 hrs per week to 39 hrs per week = 33% reduction.
Stock reduction from 6.6M to 12,200 - 99.8% reduction.
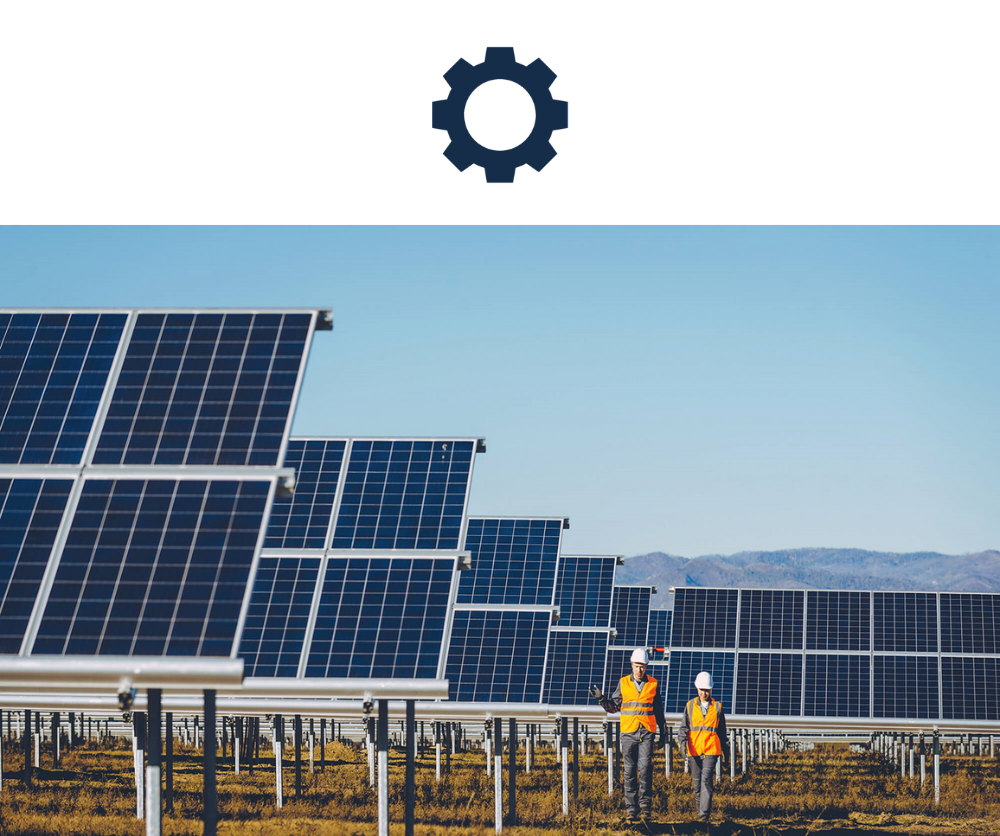
Finance Deployment (Energy Industry Sector)
10M GBP revenue from improved lifting process.
Reduced use credit notes and purchasing errors by 60%. 1.8M GBP cost avoidance.
Implementation of new processes:
Quality improved from 70% defects to 20%
Process time reduced from 16 weeks to 1 week.
Improved customer service.

Supply Chain Risk Management & Warehousing Consolidation (Energy Industry Sector)
$15.0M ($9.5M temp storage) made available on SAP to the business.
$1.4 M (Book value) Disposed.
Obsolete or Surplus Stock Removed.
$11.4M (GOI) Additional Inventory Disposed.
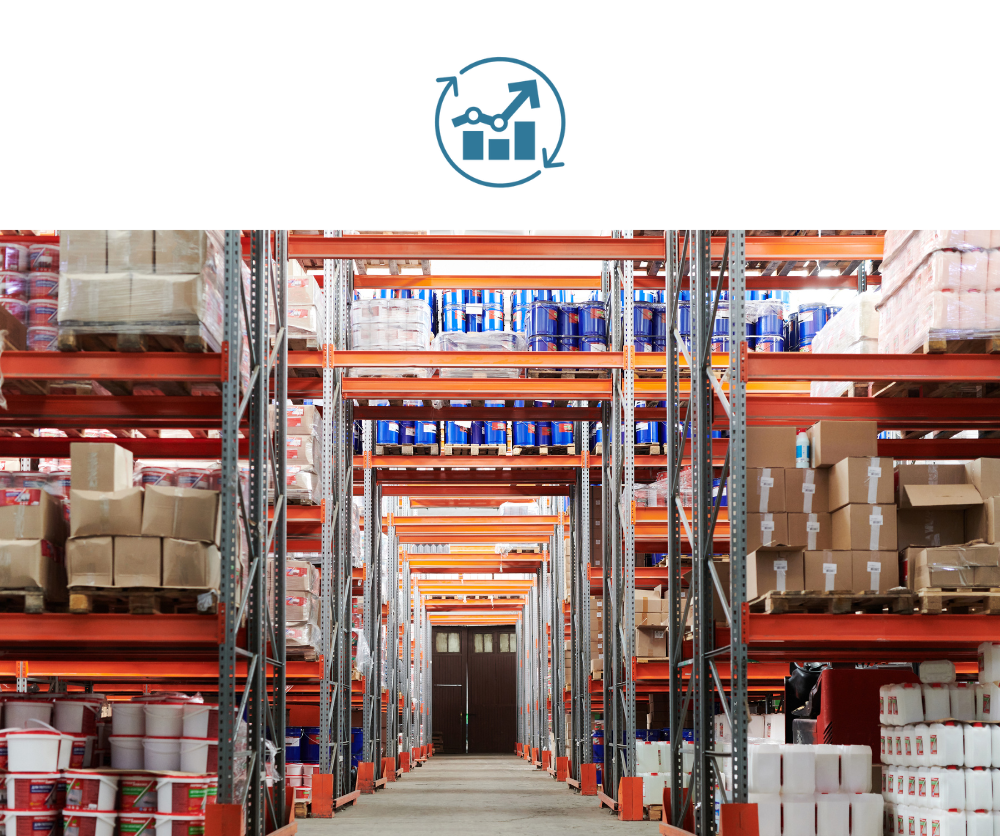
Manufacturing Programme of Improvements (Energy Industry Sector)
Production increase from 11.6M to 14.6M = 26% increase
People in this process reduced from 30 to 8 = 75% reduction
Working hours from 59 hrs per week to 39 hrs per week = 33% reduction.
Stock reduction from 6.6M to 12,200 - 99.8% reduction.
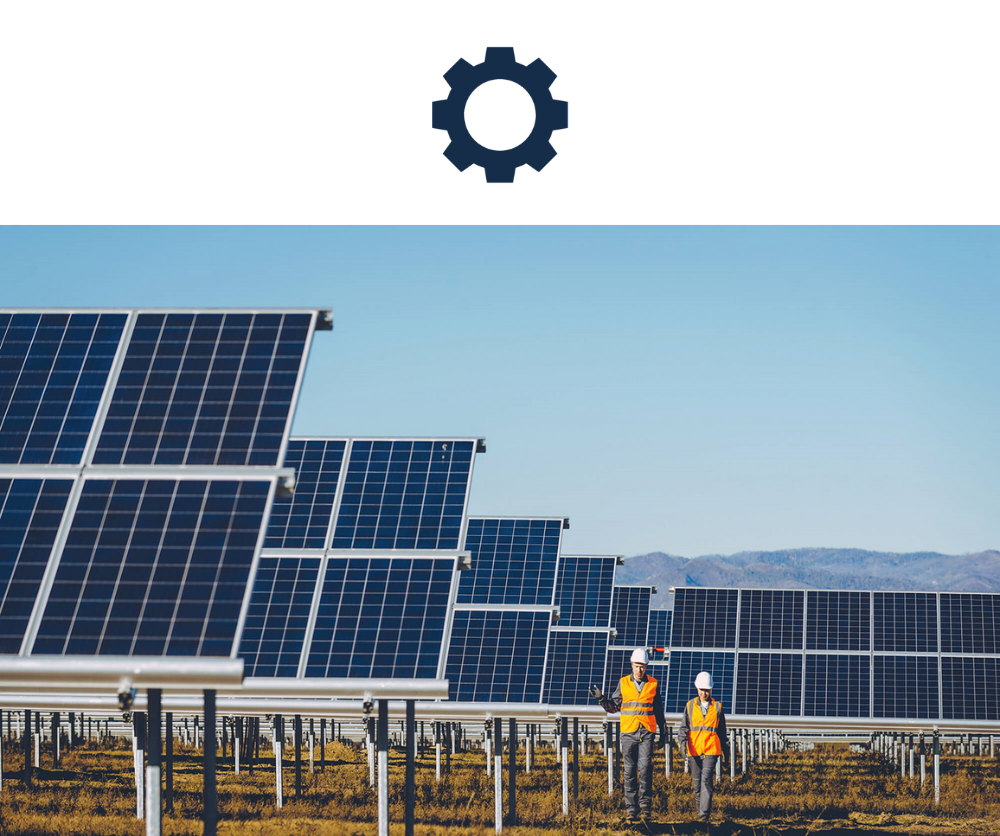
Finance Deployment
(Energy Industry Sector)
10M GBP revenue from improved lifting process.
Reduced use credit notes and purchasing errors by 60%. 1.8M GBP cost avoidance.
Implementation of new processes:
Quality improved from 70% defects to 20%
Process time reduced from 16 weeks to 1 week.
Improved customer service.
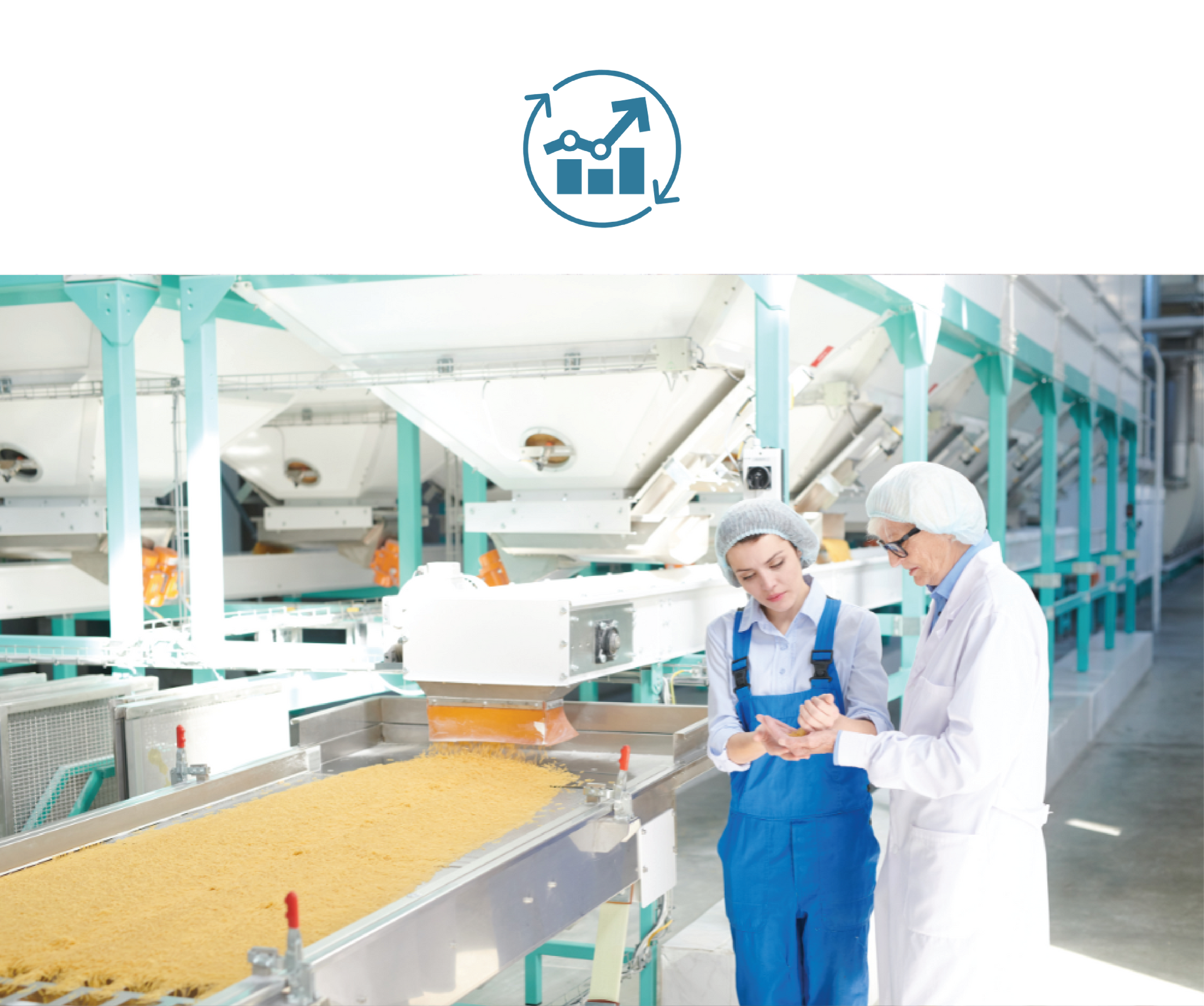
Production - Giveaway Case Study (Food Industry Sector)
65+ product codes that are bagged, projected savings for the year are estimated at £28,000+ in raw material costs and £70,000+ in sales prices.
0.95% average QA giveaway reduction on products reviewed (so far) vs target of 1% reduction.
60+ product codes to review on Bagging Lines.
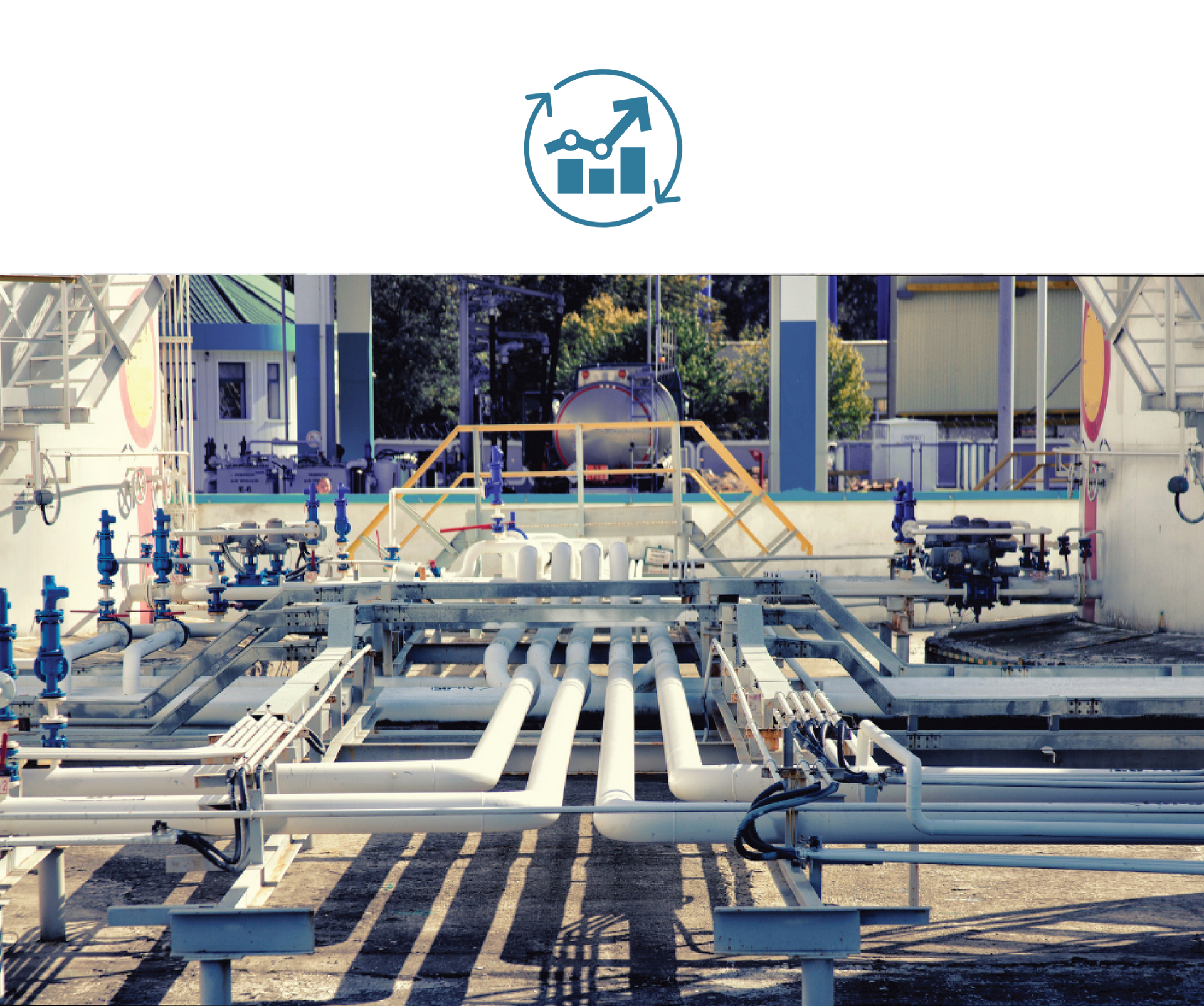
BP UK - Purchase-to-Pay (Energy Industry Sector)
£5.4M cost OPEX reduction.
2000 hrs. removed from planning activities.
£20M Reduction of Client owned materials stored.
40% Reduction in warehouse storage.
76% Improvement: 6 week planning time frame achieved.
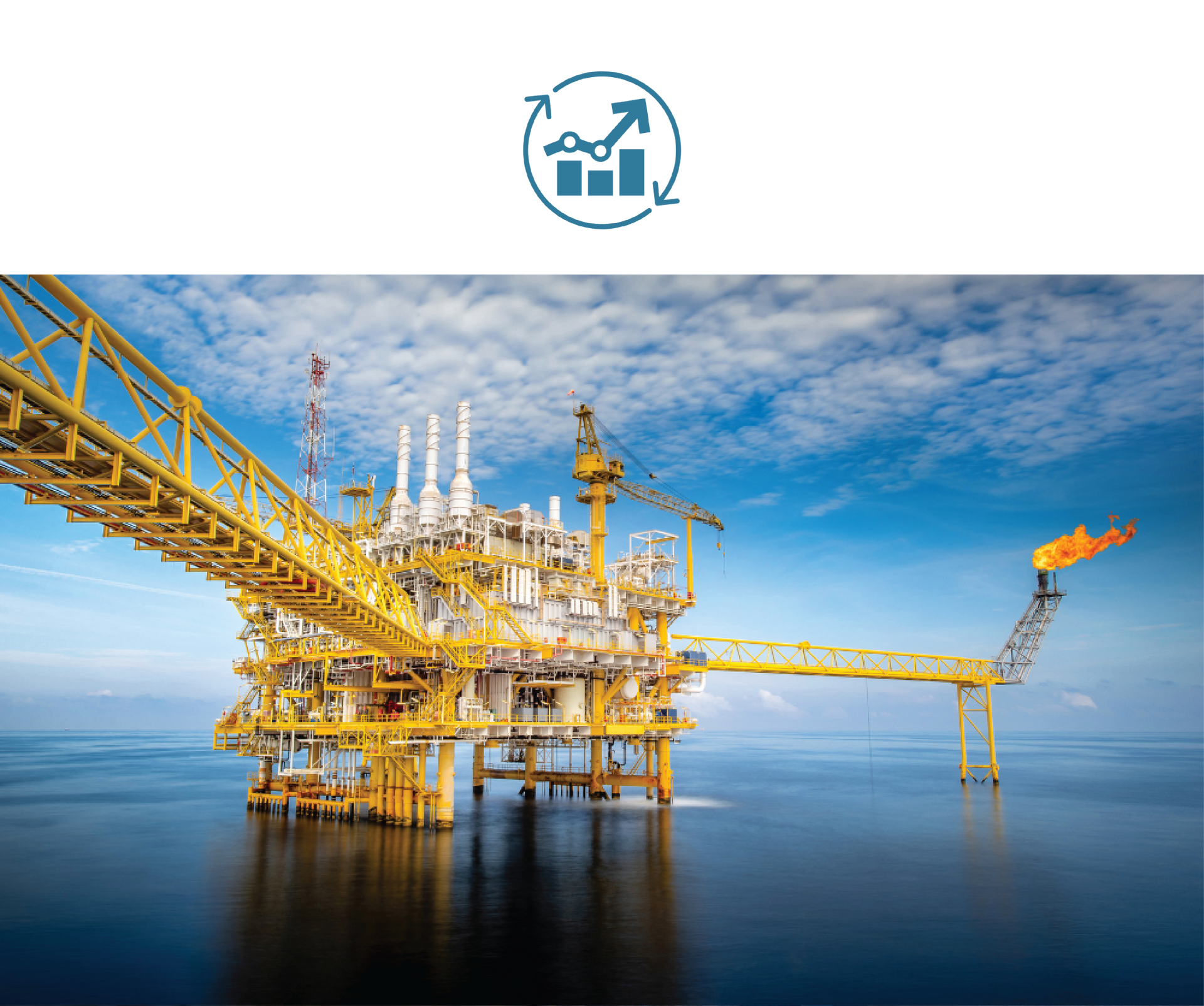
Operations Kaizen Events to support Production Challenge (Energy Industry Sector)
Temporary storage - 6.5M$.
Clair Flow Line & Installation Plan - 7.7M$.
Sea Water Lift Pump - 1639 Hrs.
Gas Turbine Setup Reduction - 2600 Hrs.
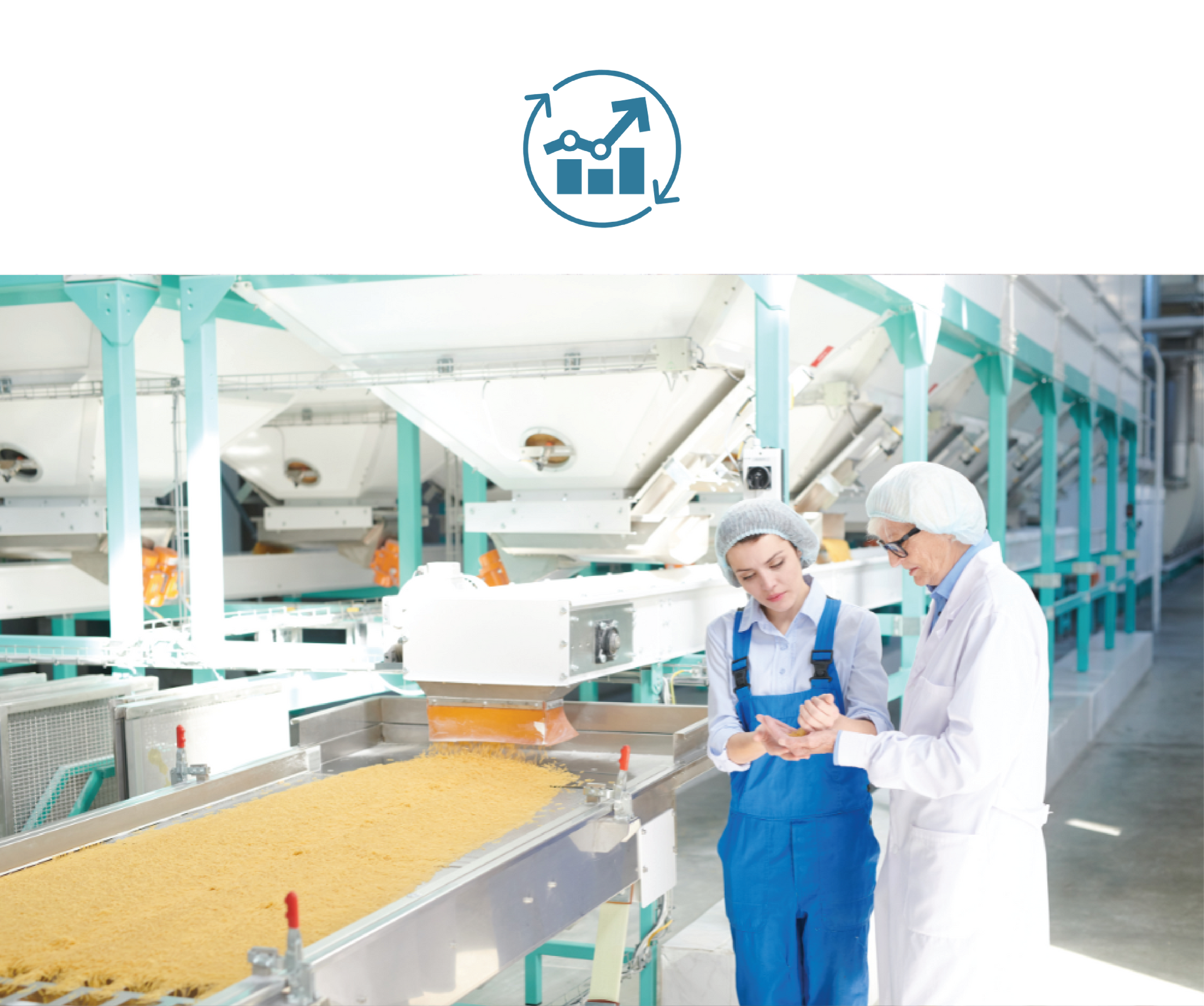
Production - Giveaway Case Study (Food Industry Sector)
65+ product codes that are bagged, projected savings for the year are estimated at £28,000+ in raw material costs and £70,000+ in sales prices.
0.95% average QA giveaway reduction on products reviewed (so far) vs target of 1% reduction.
60+ product codes to review on Bagging Lines.
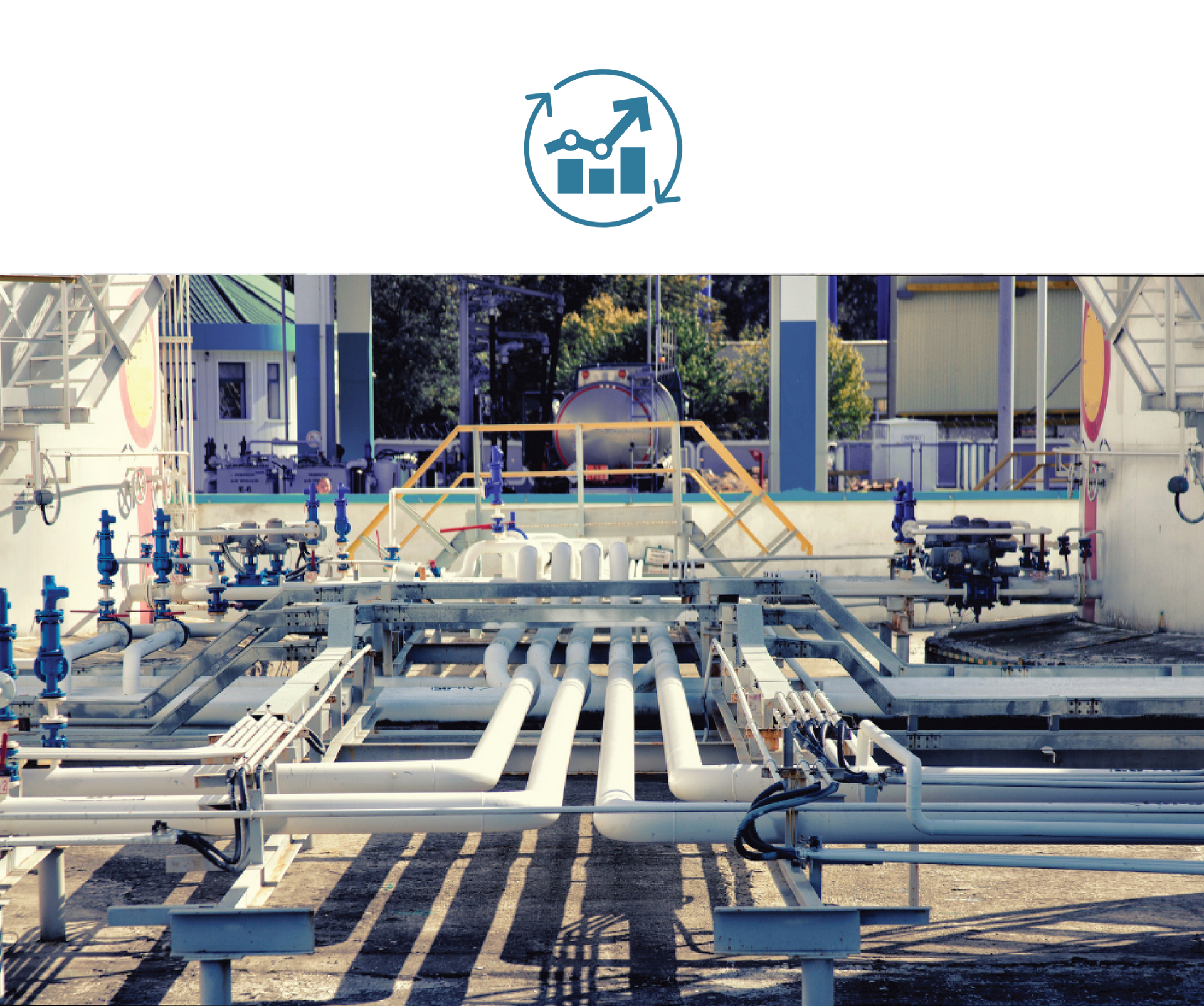
BP UK - Purchase-to-Pay (Energy Industry Sector)
£5.4M cost OPEX reduction.
2000 hrs. removed from planning activities.
£20M Reduction of Client owned materials stored.
40% Reduction in warehouse storage.
76% Improvement: 6 week planning time frame achieved.
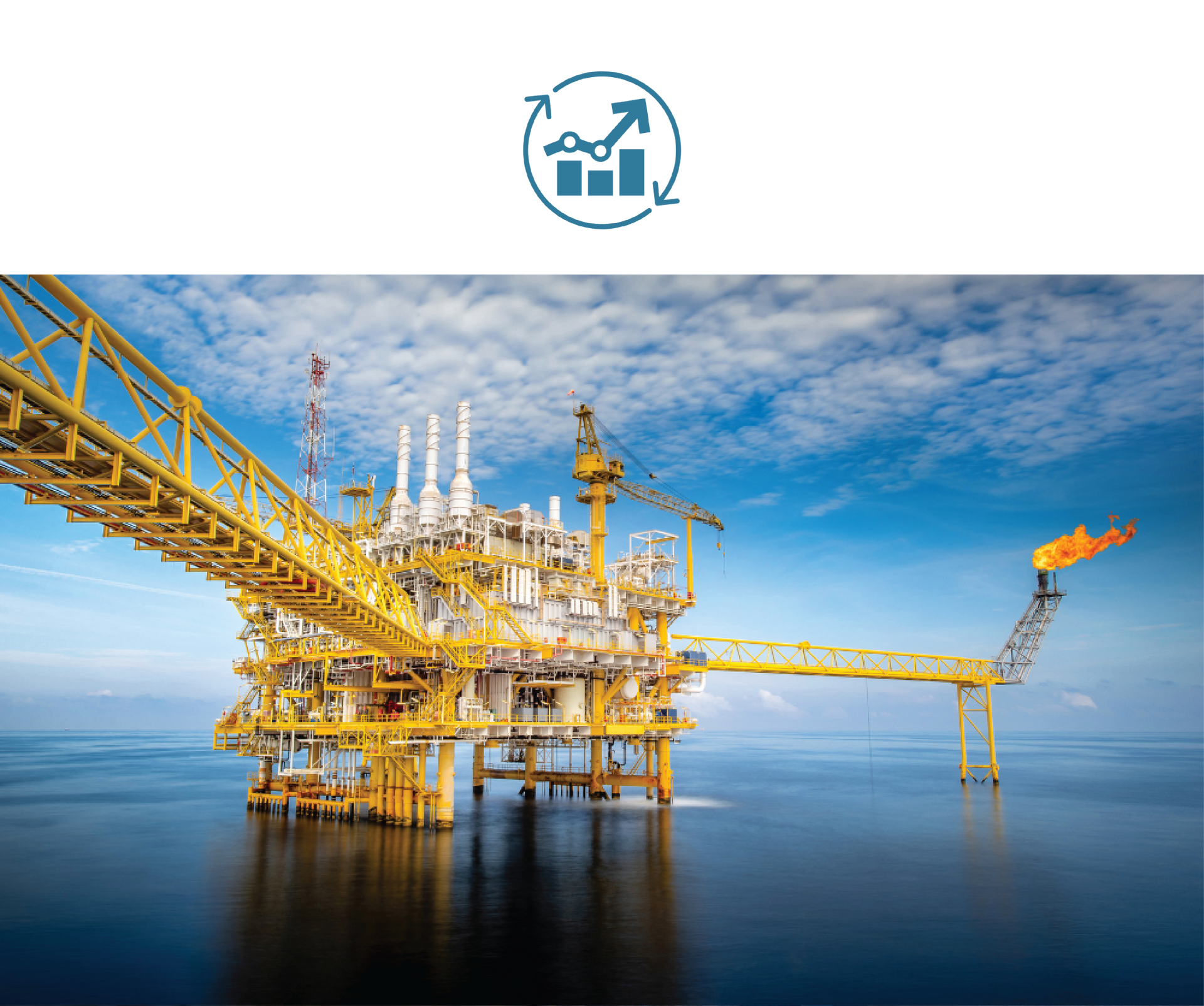
Operations Kaizen Events to support Production Challenge (Energy Industry Sector)
Temporary storage - 6.5M$.
Clair Flow Line & Installation Plan - 7.7M$.
Sea Water Lift Pump - 1639 Hrs.
Gas Turbine Setup Reduction - 2600 Hrs.
Pressure Safety Valves (Engineering Sector)
Re-use of old valves in warehouse awaiting inspection.
Inventory Reduction through implementing stocking strategy.
50% reduction in repeat planning of PSV WOs.
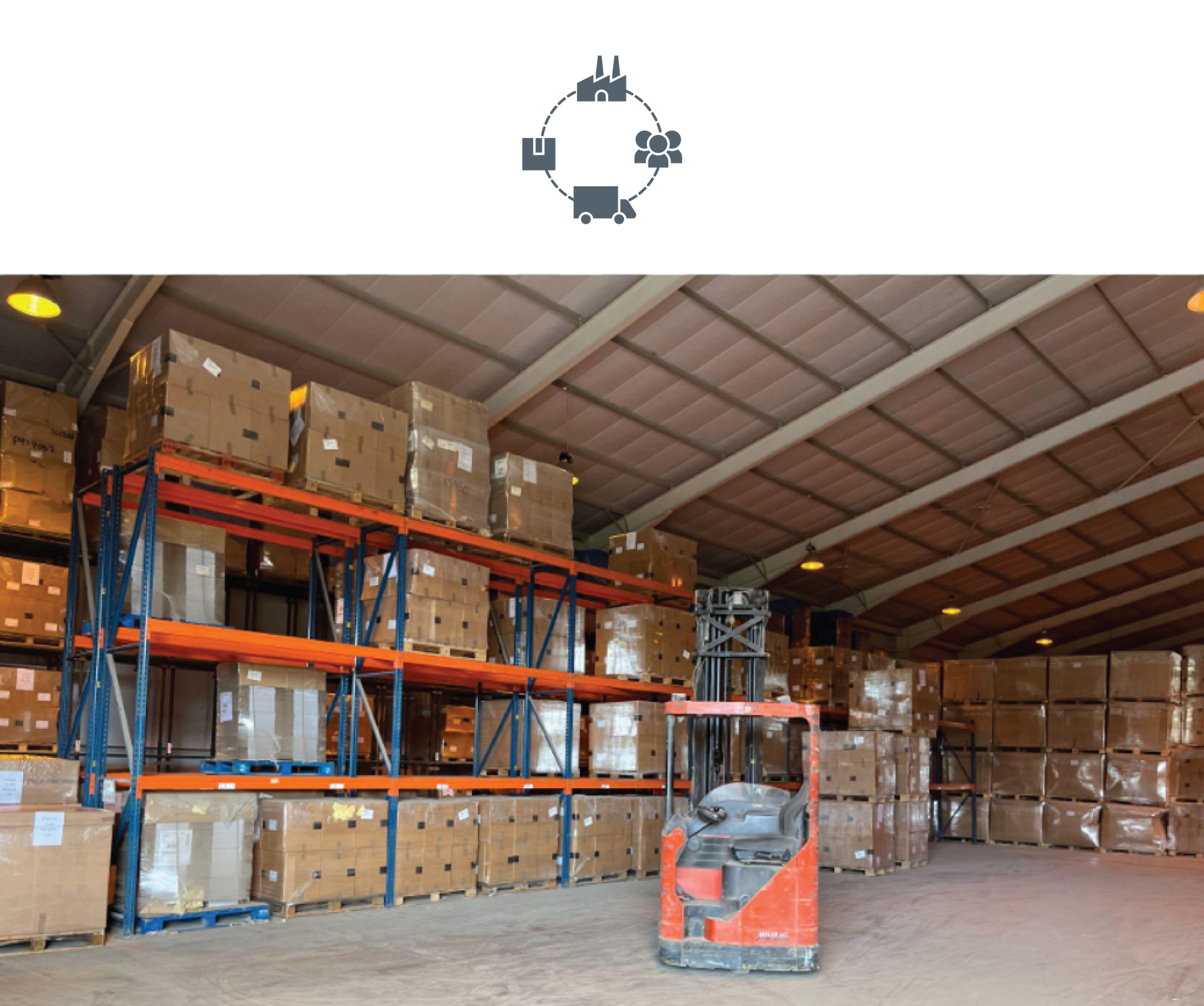
Excess Pallet Movements (Food Industry Sector)
240 pallet spaces were cleared - cost avoidance of £137,372.
Reduction in pallet movements (Jan - June) of 3,400 - nearly 50% reduction - cost saving of £24,879 over the same time period (~£50,000 per annum).
500+ issues associated to original VSM / Kaizen Event - 30 related to warehousing.
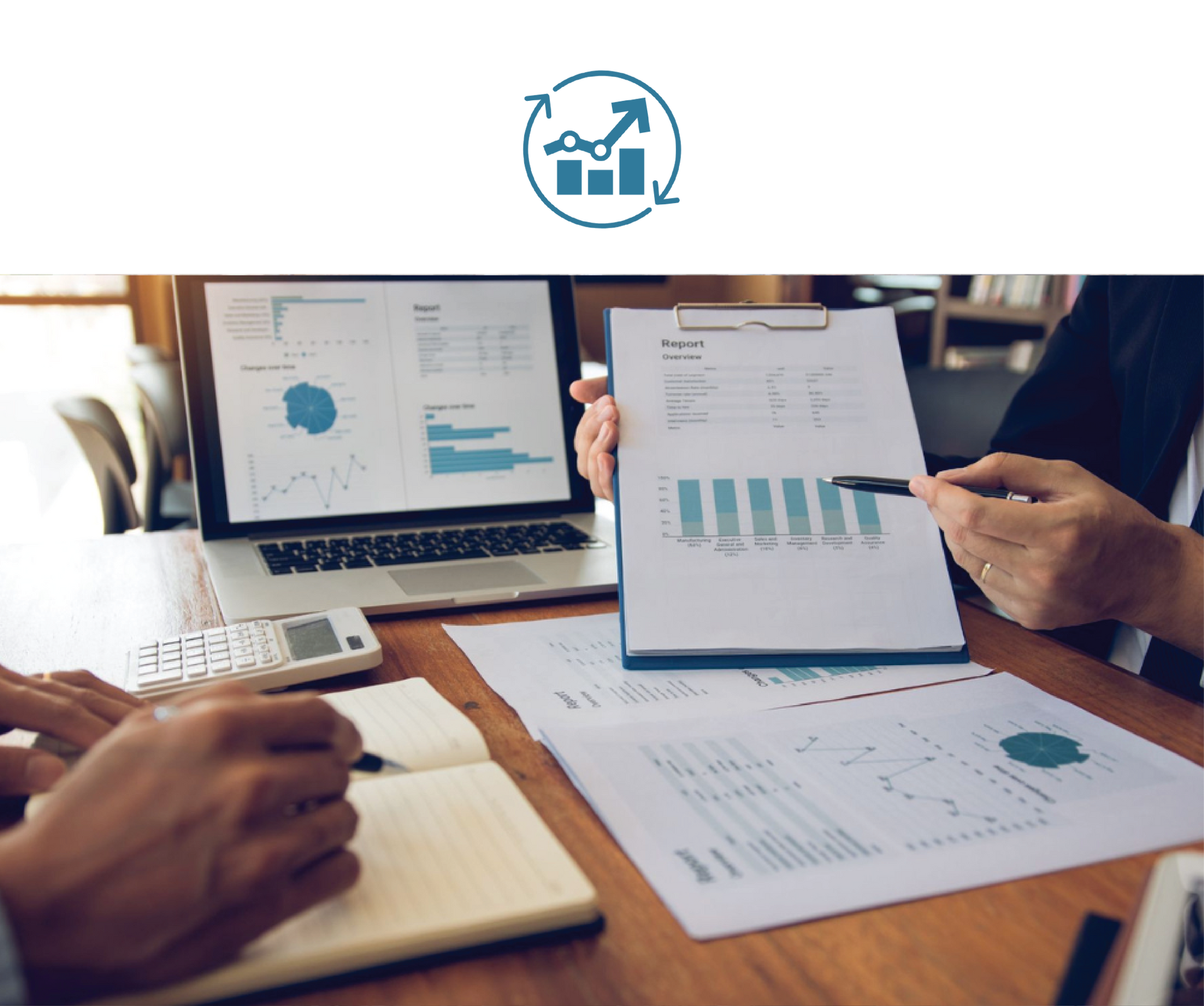
Weatherford European Accounting Centre of Excellence (Energy Industry Sector)
Standardized processes reducing waste and duplication.
In country resource constraint risk eliminated.
In country cost reduction.
Improved quality: reporting and analysis.
AP Centralisation moving responsibility back to supplier.
Hours back to business.
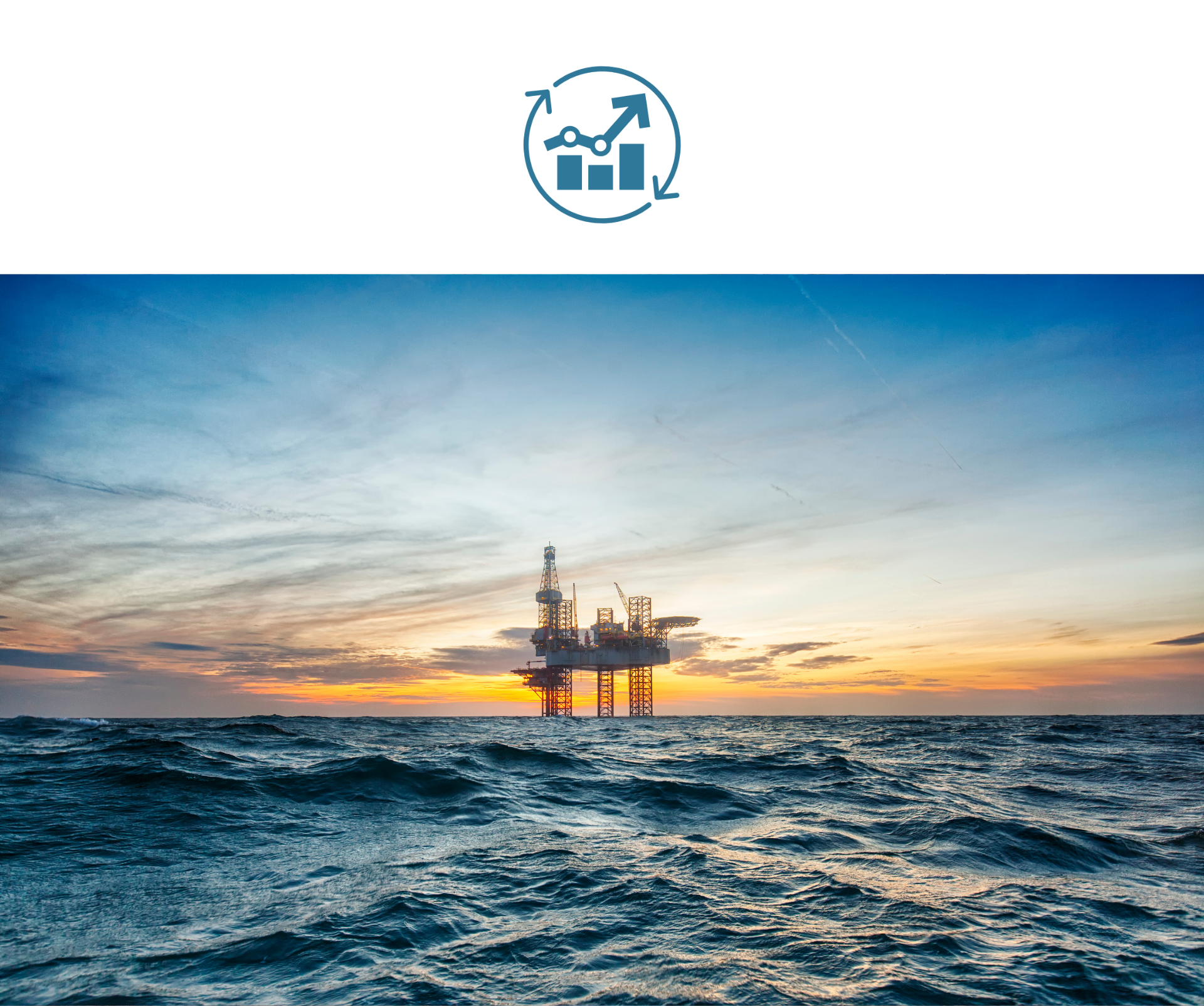
5S Materials Management Offshore Project
~37%
improvement in Stores Stock Accuracy based on Audits (opening 61%, current 98%)
£1.25M material reintegrated into stock
£1.22M material SAP corrections
22 opportunities identified, defined and closed
North Sea Asset Campaign (Energy Industry Sector)
HSE Zero Reportable Injuries
Additional +19k hrs achieved, a 24% increase on plan
Cumulative Productivity highest on record at 1.04
Kaizen SWLP: 20% Reduction on sched time. Installed additional pump
Kaizen Gas Turbine: 6 weeks, 3 days removed from plan
Finished 10 days early
Automotive Manufacturing - Lean Deployment
Cellular Units delivered quality increase from 64% to 95%
Print Set-Up reduced from 40 mins to 6 mins
60% Defects reduction during set-up
90% reduction in batch size
Combined Quality improvement & Set-Up reduction. Cost saving pa: £2.72M
Inspection defects reduced by 15%
Internal Capability Build plan executed
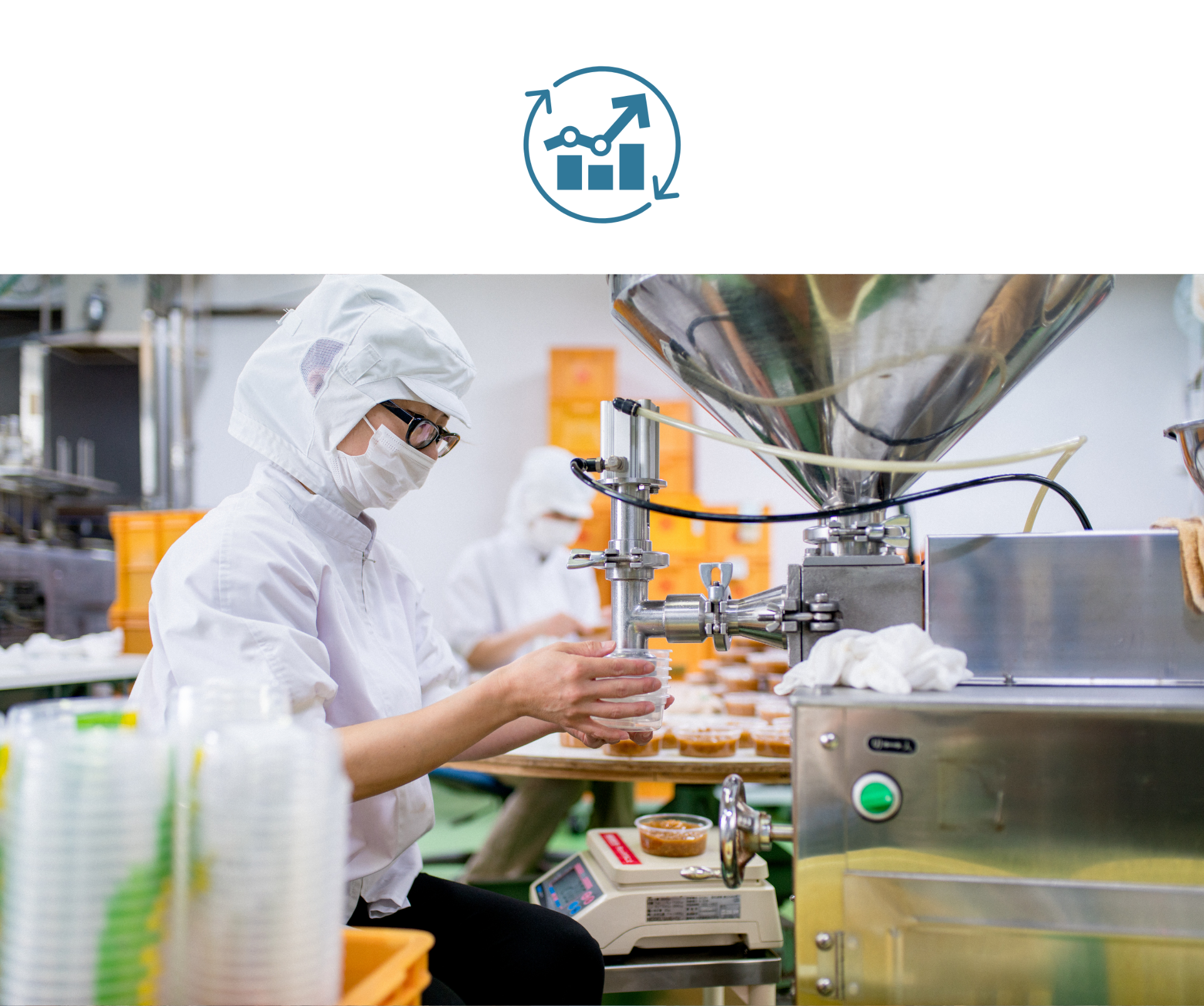
FMCG Food Manufacturing Case Study
£877,000 reduction in product giveaway through yield improvement initiatives
£480,000 in material savings via process control and waste reduction
£320,000
uplift in throughput from targeted line performance improvements
40+ internal staff trained across BT and LP programmes, strengthening CI capability
Enhancing Turnaround (TAR) Delivery in the North Sea
Aligned leadership and shared ownership of TAR goals
Improved communication between onshore planning and offshore execution
Clear visibility of progress and issues across all workstreams
Faster decision-making and issue resolution through daily huddles
On-time delivery of TAR with no reported safety incidents
Embedded culture of proactive planning and cross-team collaboration
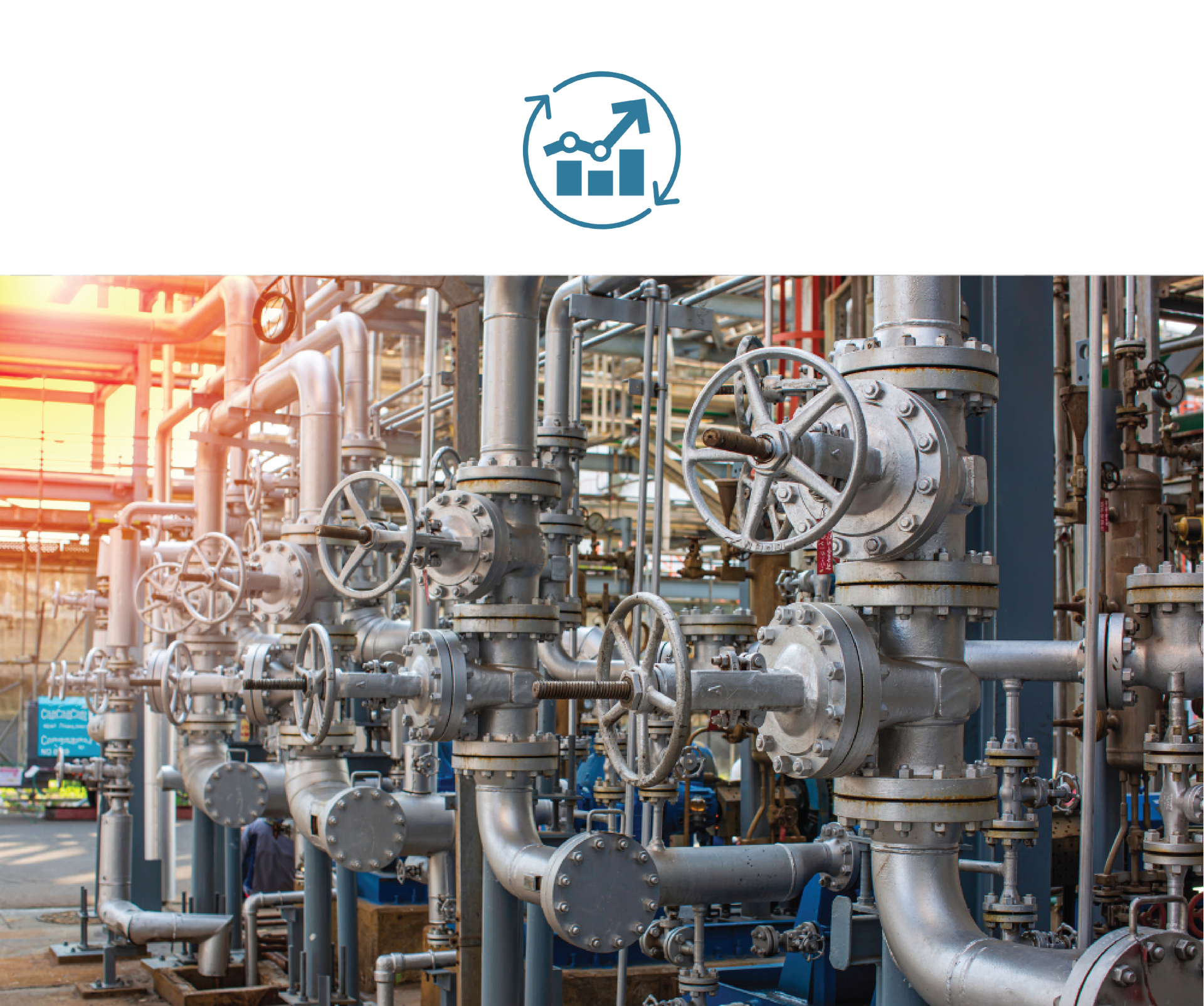
Pressure Saftey Valves (Engineering Sector)
Re-use of old valves in warehouse awaiting inspection.
Inventory Reduction through implementing stocking strategy.
50% reduction in repeat planning of PSV WOs.
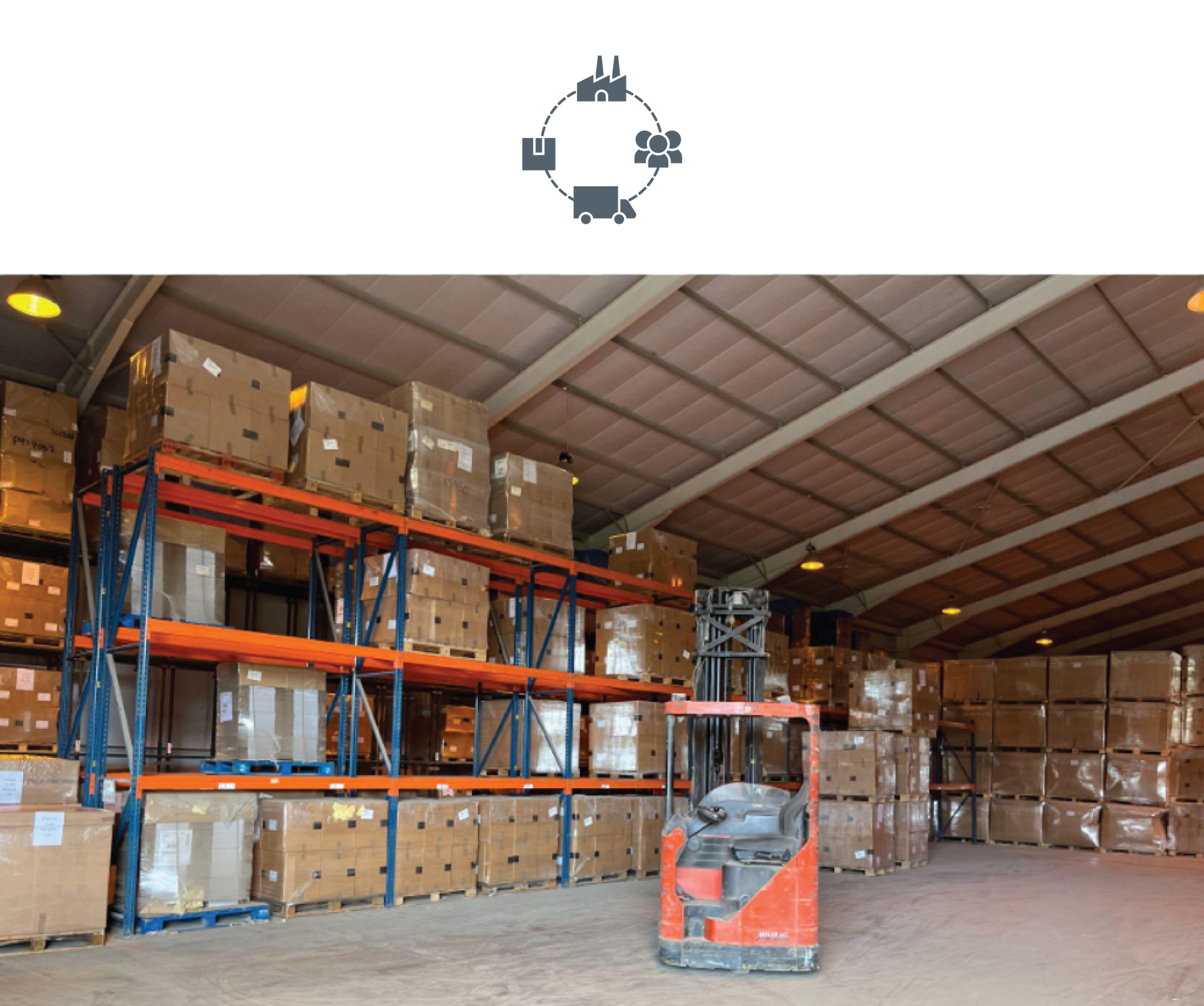
Excess Pallet Movements (Food Industry Sector)
240 pallet spaces were cleared - cost avoidance of £137,372.
Reduction in pallet movements (Jan - June) of 3,400 - nearly 50% reduction - cost saving of £24,879 over the same time period (~£50,000 per annum).
500+ issues associated to original VSM / Kaizen Event - 30 related to warehousing.
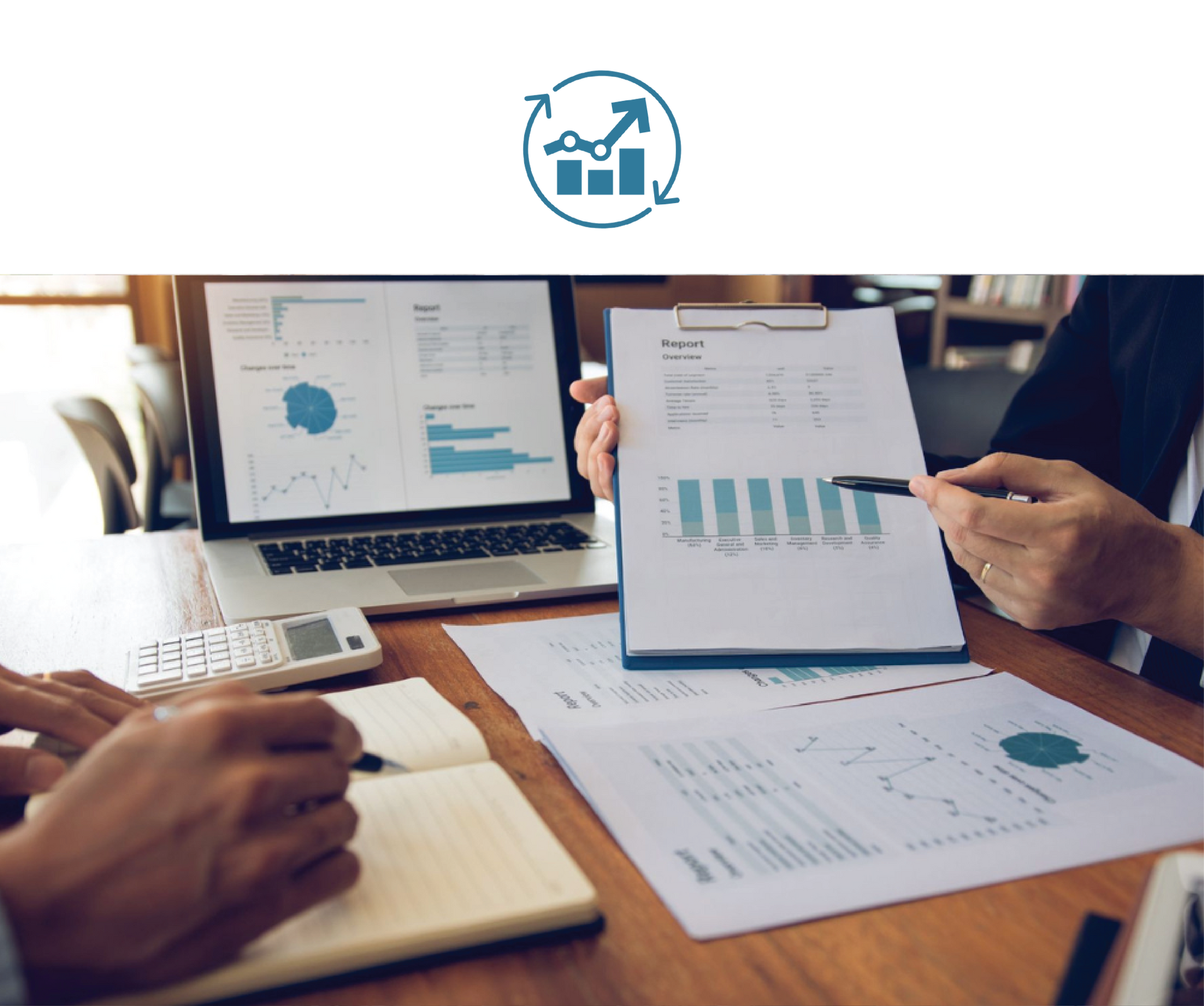
Weatherford European Accounting Centre of Excellence (Energy Industry Sector)
Standardized processes reducing waste and duplication.
In country resource constraint risk eliminated.
In country cost reduction.
Improved quality: reporting and analysis.
AP Centralisation moving responsibility back to supplier.
Hours back to business.
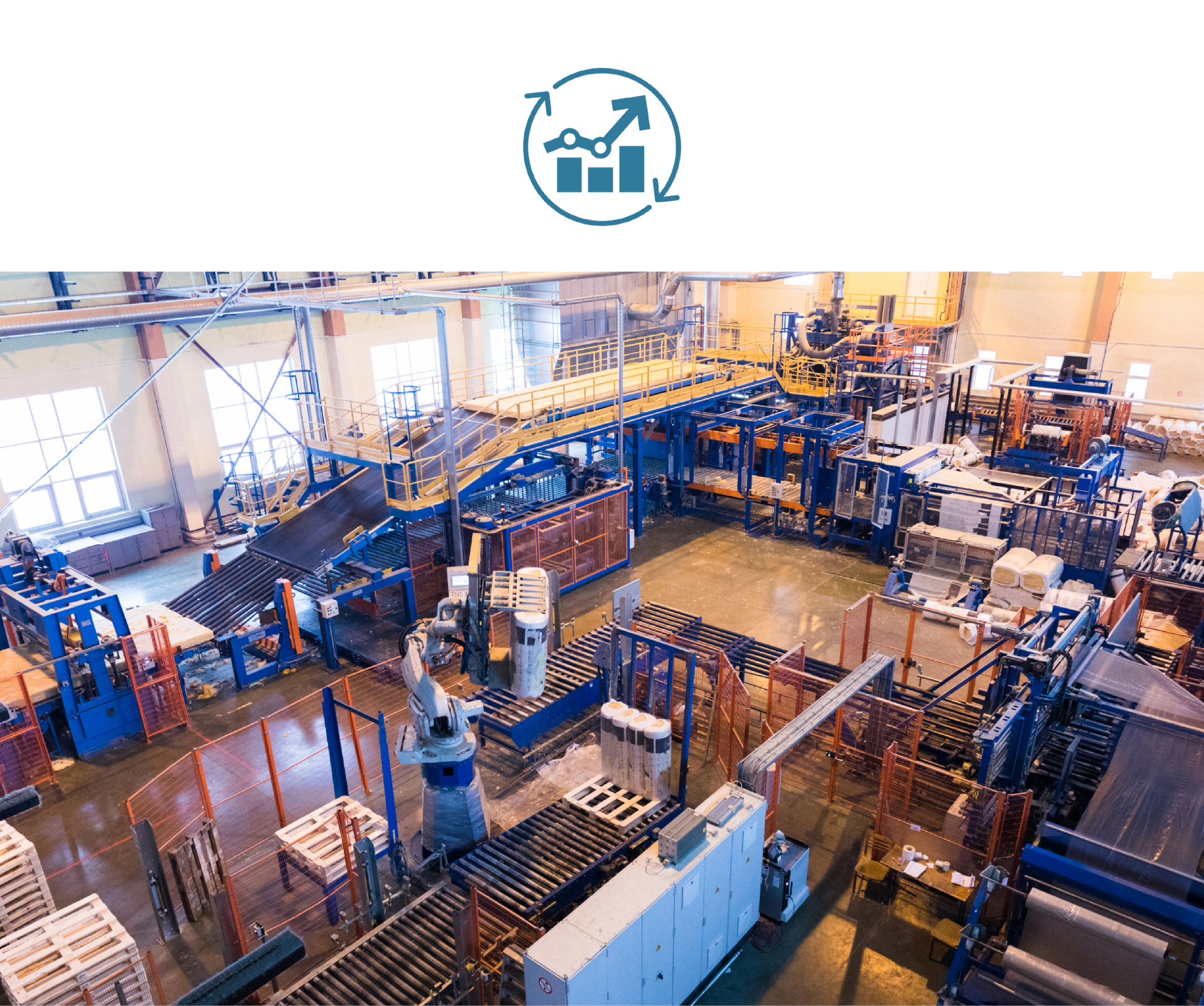
The Hidden Cost of Waste in Manufacturing — and What to do About It
Data-driven decision making, ensuring teams act on facts, not assumptions.
Ownership and coordination, so that departments align on priorities and impact.
Standardising core processes, particularly in planning, materials management, and line scheduling.
Engaged Culture (Renewables Industry Sector)
Successfully implemented 70+ effective communication systems
450+ people use effective collaboration tools daily
6,5k – 7,4k hours/pa saved ($462K) by reduced meetings
Purchase-to-Pay (P2P) (Energy Industry Sector)
5.4M cost OPEX reduction
2000 hrs. removed from planning activities
Reduction of £20M in materials stored
Reduced warehouse storage by 40%
Internal Capability Build (Renewables Industry Sector)
6 Business Agility Knowledge full day courses conducted
100+ Trained staff now lead change efforts in their own areas
14 countries supported
Supply Chain Risk Management & Warehousing Consolidation (Energy Industry Sector)
$15.0M ($9.5M temp storage) made available on SAP to the business
$ 1.4 M (Book value) Disposed
Obsolete or Surplus Stock Removed
$ 11.4M(GOI) Additional Inventory Disposed
Manufacturing Programme of Improvements (Energy Industry Sector)
Production increase from 11.6M to 14.6M=26% increase
People in this process reduced from 30 to 8=75% reduction
Working hours from 59 hrs per week to 39 hrs per week=33% reduction
Stock reduction from 6.6M to 12,200 - 99.8% reduction
Finance Deployment (Energy Industry Sector)
10M GBP revenue from improved lifting process
Reduced use credit notes and purchasing errors by 60%. 1.8M GBP cost avoidance
Implementation of new processes:
Quality improved from 70% defects to 20%
Process time reduced from 16 weeks to 1 week
Improved customer service
Production - Giveaway Case Study (Food Industry Sector)
65+ product codes that are bagged, projected savings for the year are estimated at £28,000+ in raw material costs and £70,000+ in sales prices.
0.95% average QA giveaway reduction on products reviewed (so far) vs target of 1% reduction.
60+ product codes to review on Bagging Lines
BP UK - Purchase-to-Pay (Energy Industry Sector)
£5.4M cost OPEX reduction
2000 hrs. removed from planning activities
£20M Reduction of Client owned materials stored
40% Reduction in warehouse storage
76% Improvement: 6 week planning time frame achieved
Operations Kaizen Events to support Production Challenge (Energy Industry Sector)
Temporary storage - 6.5M$
Clair Flow Line & Installation Plan - 7.7M$
Sea Water Lift Pump - 1639 Hrs
Gas Turbine Setup Reduction - 2600 Hrs
Pressure Saftey Valves (Engineering Sector)
Re-use of old valves in warehouse awaiting inspection
Inventory Reduction through implementing stocking strategy
50% reduction in repeat planning of PSV WOs
Excess Pallet Movements (Food Industry Sector)
240 pallet spaces were cleared - cost avoidance of £137,372
Reduction in pallet movements (Jan - June) of 3,400 - nearly 50% reduction - cost saving of £24,879 over the same time period (~£50,000 per annum)
500+ issues associated to original VSM / Kaizen Event - 30 related to warehousing
Weatherford European Accounting Centre of Excellence (Energy Industry Sector)
Standardized processes reducing waste and duplication
In country resource constraint risk eliminated
In country cost reduction
Improved quality: reporting and analysis
AP Centralisation moving responsibility back to supplier
Hours back to business
The Hidden Cost of Waste in Manufacturing — and What to do About It
Data-driven decision making, ensuring teams act on facts, not assumptions.
Ownership and coordination, so that departments align on priorities and impact.
Standardising core processes, particularly in planning, materials management, and line scheduling.