FMCG Food Manufacturing Case Study
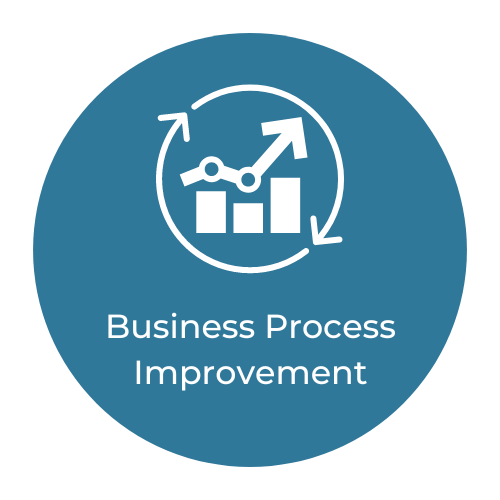
about this project
This multi-year programme supported a major UK-based FMCG food manufacturer in transforming both operational performance and internal capability. Faced with inconsistent standards, limited structured problem-solving, and a reliance on external improvement support, the business partnered with PBI to build sustainable, in-house improvement capability.
Our approach combined Business Transformation training for senior leaders with Lean Practitioner training for delivery teams, all supported by embedded coaching at site level. This dual-track model enabled leaders to take ownership of strategic improvements while frontline teams drove day-to-day operational change.
Over 40 employees were trained, more than 30 improvement initiatives were launched, and a culture of daily performance management and structured problem-solving was embedded across functions - leading to a total of £4.7M in cost savings across yield, waste and throughput improvements.
Key Project Summary "At a glance"
Project Scope
- Multi-site FMCG food manufacturing environment
- Focus on operational consistency and performance uplift
- Leadership development and culture change as enablers
- Internal capability building across senior and frontline levels
- Targeted improvement activity across waste, yield, and throughput
- Long-term coaching support embedded on-site
Improvement Strategy
- Business Transformation training for senior leaders to drive sponsorship and alignment
- Lean Practitioner training for frontline teams to build problem-solving skills
- Site-based coaching to support delivery of improvement initiatives
- Implementation of structured daily performance management routines
- Introduction of visual management and tiered accountability processes
- Prioritisation of high-impact projects aligned to strategic goals
Benefits Delivered
- £877,000 reduction in product giveaway through yield improvement initiatives
- £480,000 in material savings via process control and waste reduction
- £320,000 uplift in throughput from targeted line performance improvements
- Embedded daily performance routines with measurable team-led improvements
- 40+ internal staff trained across BT and LP programmes, strengthening CI capability
- Sustainable culture shift enabling continued cross-functional improvement