Manufacturing Programme of Improvements
(Energy Industry Sector)
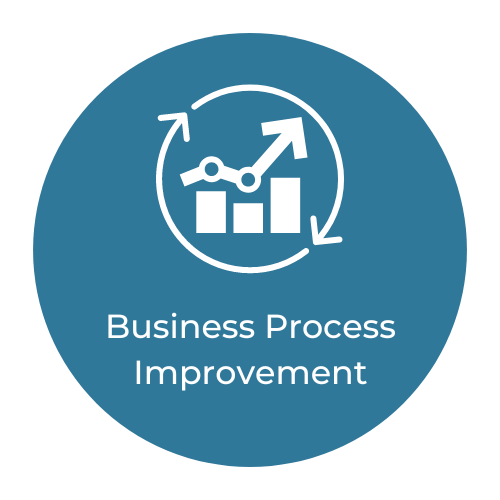
about this project
The company, a FTSE 100 disinfectant manufacturer had expanded in size in a range of high volume products. They were experiencing massive growth in both their existing products and in a range of new products that were proving to be very successful in the marketplace.
The manufacturing facility expanded to keep pace with the growth but the manufacturing process and approaches, had not changed for many years.
The key objectives of the engagement were:
- Remove manual handling were possible
- Increase equipment utilisation
- Increase productivity per operator
- Reduce floor space for further expansion plans
Key Project Summary "At a glance"
Project Scope
- Remove manual handling where possible
- Increase equipment utilisation
- Increase productivity per operator
- Reduce floor space for expansion plans
Improvement Strategy
- Workplace organisation using 5S
- Kaizen Events for rapid change
- Set up Reduction techniques
- Daily Stand up meetings
- Introduction of Quality in Station-Statistical Process Control(SPC)
- Training of staff for sustainability
- Visual Management
Benefits Delivered
- Production increase from 11.6M to 14.6M=26% increase
- Using 50% less equipment
- People in this process reduced from 30 to 8=75% reduction
- Working hours from 59 hrs per week to 39 hrs per week=33% reduction
- Removal of 100% Manual handling
- Stock reduction from 6.6M to 12,200 - 99.8% reduction
Additional deliverables as a consequence of improvements
- Implementation of new product line for £30K compared to £250K=88% reduction in investment
- Used existing employees-no recruitment
- Used equipment released from production improvements