BP UK - Purchase-to-Pay (Energy Industry Sector)
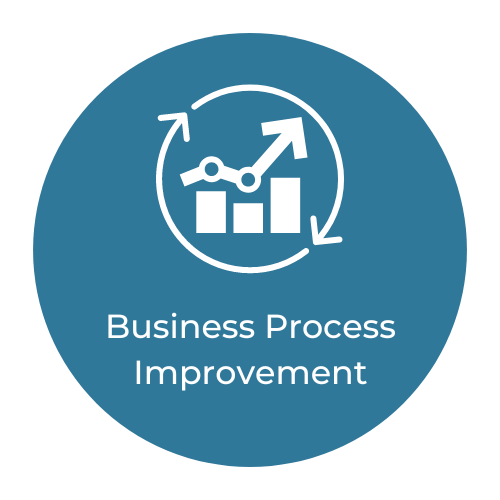
about this project
Our Client, one of the largest Oil and Gas producers in the North Sea required a full review of their entire Purchase to Pay process. They had a highly complex supply chain management program covering many 1000’s of individual suppliers. Their ERP system based on SAP was highly layered and complex.
The region also included the management of warehousing locations (client and vendor owned) with over 50 individual sites. This added a great deal of complexity to the supply chain management process with each site a mixture of client owned / vendor owned stock, quite often managed by different material management software packages.
The opportunity - to review the entire P2P process and look for potential areas for improvement, better integration with suppliers, reconciliation of systematic Vs physical material counts in multiple sites. We also included a review of how client and vendor owned stock was identified, processed and stored.
Key Project Summary "At a glance"
Project Scope
- The scope involved a complete review of Supply Chain and business processes that cover: requesting / requisitioning, purchasing, receiving & storage, paying for and accounting of all materials within the regions scope of control.
- Focus areas included both Client owned and Vendor Owned or controlled stock.
- In service of operations the primary objective was:
- The correct material
- At the correct time
- In the correct place
- In the correct packaging
- In the correct quantities
Improvement Strategy
Deployed Methods:
- Operations and Procurement dual Sponsorship of all Improvement Projects
- Stakeholders included key vendors
- Agreed Lean & Agile program of activities
- Workplace organisation using 5S
- Kaizen Events for rapid change
- Training of staff for sustainability
- Performance Management
Benefits Delivered
- £5.4M cost OPEX reduction
- 2000 hrs. removed from planning activities
- £20M Reduction of Client owned materials stored
- 40% Reduction in warehouse storage
- Capability to Replan Work if not started, removing need for child work orders
- Single Package Material for all work order, no split materials sent to site
- End user packaging now implemented as standard / rather than warehouse
- 76% Improvement: 6 week planning time frame achieved. Compared to 300 days previously.
- Aligned buying department with end user. Materials now ordered with lead time +