Production - Giveaway Case Study
(Food Industry Sector)
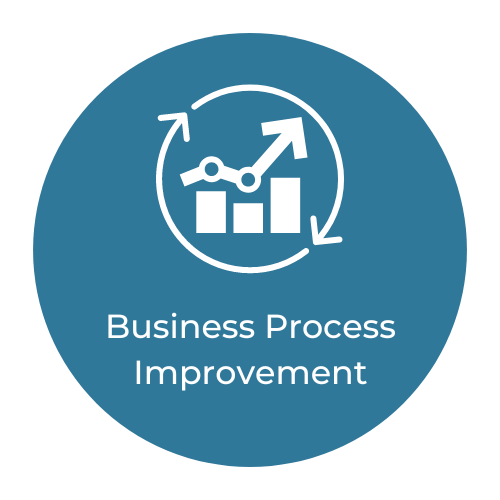
about this project
The client is a major Scottish food manufacturer, supplying goods globally. PBI were employed to provide proven Lean project delivery expertise and work as an integrated partner with the Leadership and site teams, with a focus on the Production side of the business.
One objective was to reduce the giveaway on each bagged product by adjusting the scale weights and tolerances on the bagging machines. Giveaway can be defined as overfilling a bagged product above its Net Weight.
The client recognised the benefits of using a Lean and Agile approach to baseline the problem, evaluate the extent of the issue and devise a structured process to improve Giveaway on all bagged products across the site, collaborating with a team from two factories.
The requirement to develop a more standardised process for future activity and a monitoring process for sustainment was also identified.
Effective sponsorship was critical as the team involved based on the activity scope involved Factory Managers across multiple factories, Charge Hands, Machine Setters and Engineers. Communicating the impact that Giveaway can have on the business was an essential part of the initial phase of the event.
The key objectives of the engagement:
- Reduce Giveaway on Bagged Products by an average of 1%
- Improve Giveaway data reliability through increase in data collection
Key Project Summary "At a glance"
Project Scope
- Aim of project was to decrease the amount of Giveaway on bagged products in 2 Factories
- Aim to roll-out to remaining factories after initial improvement in place
- Implement real-time process Improvements
- Identification of further process Improvements required to sustain Giveaway reductions
- Effective Teamwork & Engagement
- Internal Capability Build
Improvement Strategy
- Standardised process across both factories for Bagging Machine set-up during shift change and product change for Machine Setters & Charge Hands
- Additional training days for Machine Setters across both factories
- Checkweigher plug-in used to track all products made to increase giveaway data reliability
- Communications to Management, Factory Managers and factory staff before, during and after event on the importance of reducing giveaway across all factories
Benefits Delivered
- 65+ product codes that are bagged, projected savings for the year are estimated at £28,000+ in raw material costs and £70,000+ in sales prices.
0.95% average QA giveaway reduction on products reviewed (so far) vs target of 1% reduction.
60+ product codes to review on Bagging Lines