From Training to Transformation, in Renewables
Over 320 staff across 13 countries trained, 75% framework adoption and more than 6,500+ hours saved annually, these headline results demonstrate how a two-phase approach to transformation delivers lasting impact in the Renewables sector. By first equipping teams with Lean and Agile tools and then activating a culture of continuous improvement, organisations can turn classroom learning into real-world gains.
The Challenge, Reimagined
Many Renewables businesses struggle with knowledge gaps and disconnected teams. Leaders recognise the value of Lean and Agile practices yet lack a structured way to spread those skills beyond initial workshops. Improvement efforts often stall in silos, slowing decision-making and squandering opportunities for efficiency and innovation.
Phase 1, Building Internal Capability
The journey begins with targeted, SQA-accredited training programmes, our SCQF Level 9 Business Transformation and Level 7 Lean Practitioner courses. Participants dive into interactive simulations, understanding leaderships role in transformation, workplace organisation using 5S, daily huddles and campaign room coordination, to name a few. They emerge certified practitioners with practical toolkits for orchestrating change. Post-course (optional) coaching ensures those skills take root, guiding teams through real-world application and reinforcing new ways of working.
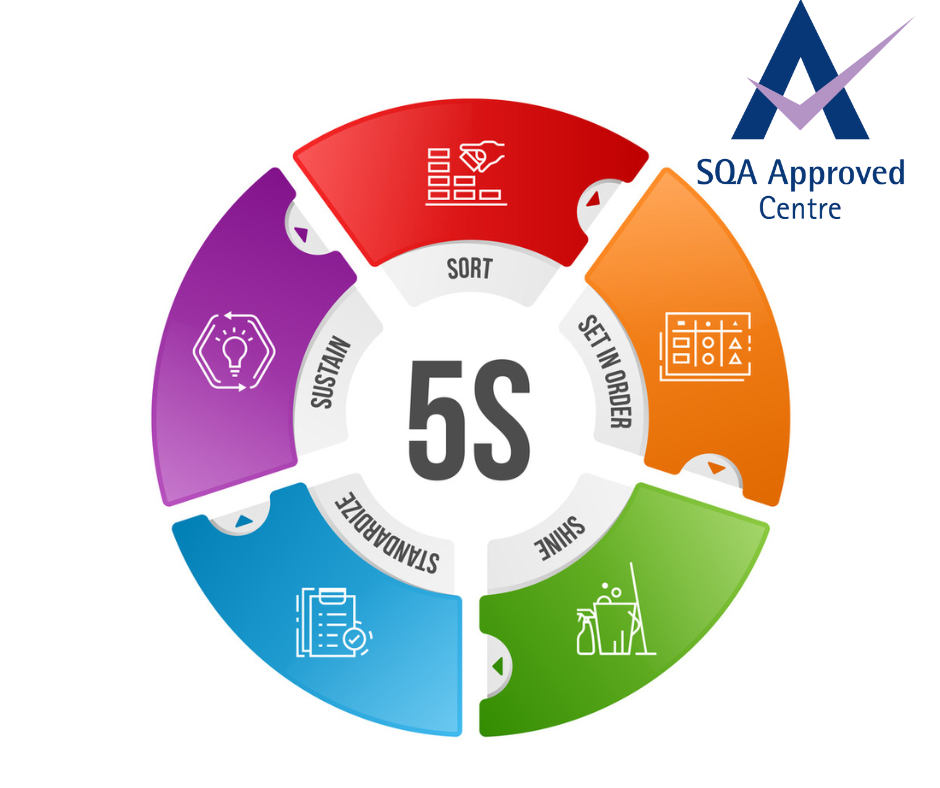
Phase 2, Activating an Engaged Culture
Graduates become catalysts for cultural change. Across multiple sites, teams launch daily huddles around visual management boards, surfacing issues before they escalate and develop shared ownership of safety and performance. Cross-functional campaign rooms become live command hubs where engineers, operations and safety experts collaborate to solve complex challenges in real time. Employee-led Kaizen events uncover quick-win improvements, proving that small, focused events yield significant results when owned by empowered teams.
Real-World Outcomes & Voices
These combined efforts delivered transformative results:
- 75% of staff adopted new frameworks consistently
- 6,500 to 7,400 hours saved each year, equating to a value of over £460,000
- 90% of participants would recommend the new methods to colleagues
One senior operations manager reflected:
“Seeing teams across three continents run huddles and Kaizen events as second nature proved that we’d truly shifted from one-off projects to an ingrained culture of improvement.”
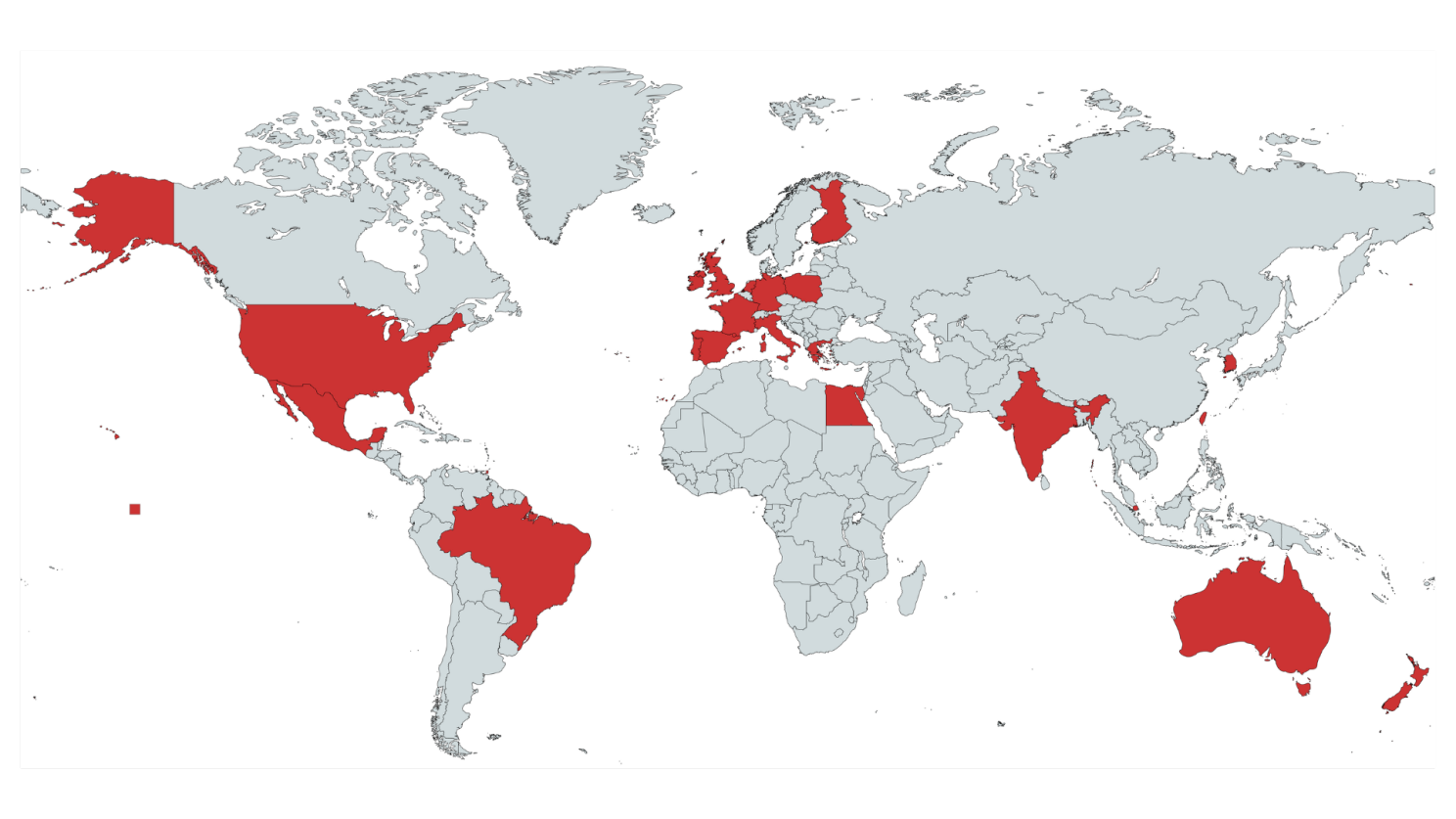
Full-Circle Impact
This full-circle model—training, coaching and cultural activation - turns theory into practice and practice into performance. Renewables organisations gain not only certified expertise but also the engaged, cross-functional collaboration needed to sustain continuous improvement. By building capability first and then igniting culture, companies unlock real savings, boost safety and accelerate innovation.
With proven frameworks and hands-on coaching, any Renewables team can replicate this cycle, embedding lasting change that propels both efficiency and growth.